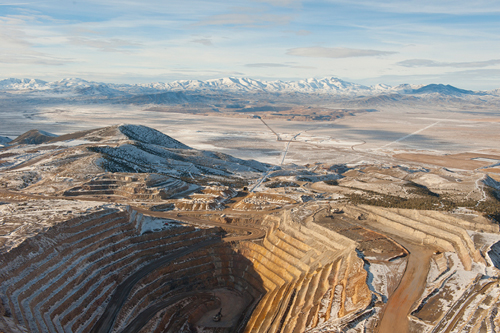
Over recent years, Cortez Hills has yielded well over a million ounces of gold annually, in the first quarter of last year at a cash cost of $308 an ounce, well below industry averages of between $400 and $500. The key to the success of this operation lies in the nature of the deposit, says George Fennemore, Barrick’s Manager of Corporate Social Responsibility and regional permitting specialist for the company. Like most Nevada mines, Cortez contains large deposits of ‘invisible’ gold, where the ore holds microscopic particles rather than veins or nuggets of gold. But to understand the present day deposit it is necessary to look at its history.
Mining in the Cortez district began in 1862, says Fennemore. “The mining authorization for some of the claims out there was originally signed by Abraham Lincoln’s administration: in fact the first development was encouraged by the US government to help fund the Union effort during the Civil War.” There has been almost continuous mining in this district for 150 years, however the metal Lincoln had his eye on was silver, and silver mining continued there right up until the outbreak of World War II.
Gold mining activities started after the war, but it was not until 1962, when the United States Geological Service inaugurated a two-year pilot project at Cortez and Newmont’s nearby Carlin property to refine the application of heap leaching to these low carbon, low sulfide oxidized deposits, that the ‘invisible’ gold became commercially ‘visible’. “The process is simplified when you don’t have to deal with those refractory elements which interfere with gold production,” says Fennemore. In his opinion these studies helped to grow the industry significantly through the final two decades of the last century, particularly in the Nevada goldfields. “We developed some very innovative processes to turn this ore into gold. The cyanide heap leaching process we use was developed here at Cortez and was found to be very effective in removing microscopic gold even from low grade ore deposits, especially deposits that were oxidized – ores that do not have a lot of sulfides or carbon in them.” The Cortez deposits tend to be low in sulfide and carbon deposits and very conducive to heap leaching.
Not all the gold in the Cortez district is held in these oxidized deposits, but a significant proportion of it is, and there is much more of it than was ever suspected when the nearby Pipeline deposit was being mined in the 1990s using truck and shovel methods. “We have continued to look for these large scale oxidized deposits,” he explains. “They are well suited for the mining fleet and for the processing that was already available on site. By going back into productive districts and drilling a bit deeper we were able to locate the Pediment deposit back in 1999. Further drilling revealed the adjacent and larger Cortez Hills deposit. That was when we finally understood that there was a large gold deposit at depth.” A minority of the gold at Cortez Hills is indeed found in refractory rock. This is transported 75 miles to the company’s specialized mills at its Goldstrike property to the north of Elko – this might seem an expensive option, but it makes sense when one considers that construction of a new refractory mill would cost upward of a billion dollars.
Barrick took six years to complete its drilling program and establish a deposit in the region of 9 million ounces coming in at a very satisfactory grade, with some areas exceeding one once per ton of ore. The permitting process began in 2005 with applications to both federal and state agencies, and the operating permit was finally received in November 2008.
The entire process was complicated by the fact that the area became the focal point for a Native American rights organization’s struggle over land that is now managed by the US federal government. Besides gold, the area was also rich in historical and cultural resources. While Cortez Hills contained no Native American settlements as such, it was located on traditional migration routes. Artifacts were found in their thousands, dating back thousands of years. “We executed one of the largest archaeological programs that had ever been done in the State of Nevada aiming to characterize, document and preserve the archaeology and history through that area.” Over eight months the site was populated by archaeologists armed with trowels and going inch by inch across the area of the proposed mine. In all, nearly 400,000 artifacts were recovered, many from historic mining in the area. Cataloguing these items was a massive task for the Nevada State Museum which continues to stabilize, curate, and preserve them for posterity.
There’s never a mining development where there are not some objections from community, environmental and commercial interests, and Cortez Hills was no exception. Barrick’s legal success over objections gave no particular cause for satisfaction and George Fennemore in fact sees the dialogue as a prime way to engage legitimate concerns and hopefully allay them. “Because we utilize public land for our mining, this gives the opportunity for any interested party to comment. Anyway the dialogue is not just about our mining operation but in general how the government handles resources.” This is a particularly big issue in Nevada where 90 percent of the land is Federal Government owned. Cortez is the largest mining operation on federal land in the USA and the main permitting process handled through the US Bureau of Land Management is bound to attract considerable public comment. That may not always be comfortable but it does provide a forum. In the end, local interests should receive primary consideration in view of the undeniable economic boost the project and all its associated activity generates.
By midsummer of 2009 construction was in full swing, using a 78-cubic-yard P&H 4100, multiple 57 cubic-yard P&H 2800 shovels and a fleet of 27 400 tonne Liebherr haul trucks. Though it took till the end of that year before the ore body was uncovered and gold recovery could commence. This was a fast track project. It took just under a year to get from virgin ground to the ore body, says Fennemore. “We process the ore from both the open pit and the underground mine below it at our existing facilities which are about nine miles away from the pit itself, so we opted to build the longest conveyor in Nevada rather than truck ore from the pit.”
The conveyor designed and supplied by ThyssenKrupp Robins can transfer 1,000 tons per hour from the Cortez Hills to the existing heap leach facility – it includes a belt feeder and five conveyors. A 90 foot long variable speed belt feeder transfers primary crushed ore to the first of the 5 conveyors. The most complex conveyor of the system is the seven mile long regenerative overland conveyor that runs at 900 feet per minute with a 2 mile long downhill section with a descent of 900 feet. A unique control system was developed to achieve the right belt tension between the drives. The conveyor can now transport ore from both the open pit and the underground mine which was constructed over the same period. The underground ore body is reached via twin declines at six degrees gradient, and the underground mine has been designed so that its highest levels will eventually coincide with the bottom of the open pit.
Having established that all possible work had been done to preserve the archaeology on the site it was also important to ensure that the Shoshone people who live in the area would benefit from the work being done. The area was covered with a young second growth forest, Fennemore says, and when the time came for these trees to be removed the Shoshone people were consulted and the timber made available to indigenous communities for firewood and other uses.
It is important to get interventions of this sort right, George Fennemore believes. “It is easy for a big corporation to overwhelm a small community so we work very diligently to pay attention to the land users, other water users, and employers – for example when we harvest trees we are careful to work with local woodcutters and not wipe out their business by dumping a load of firewood onto the market.” A global corporation such as Barrick has to be particularly diligent, he says, to be sensitive to the needs of local communities and local businesses and operate in ways that will not disrupt their livelihood. Many local vendors and suppliers are supported by the presence of a large operation, and many local businesses have benefited from Barrick’s policy of sourcing the maximum possible in materials and services from them.
Written by John O’Hanlon, research by Jeff Abbott