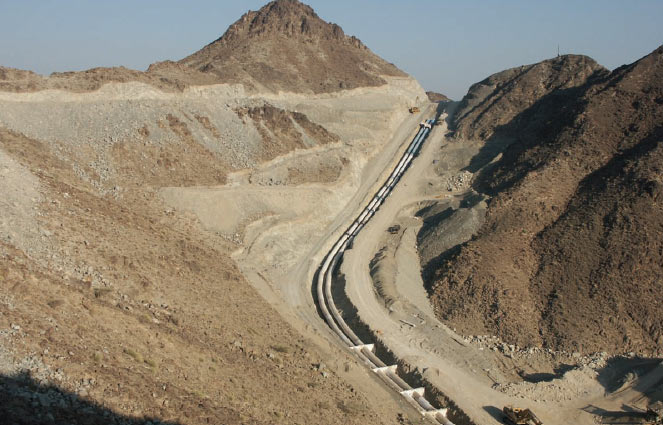
Technip Germany is part of the Paris-based Technip Group, a world leader in engineering, technologies, construction and project management for the oil and gas industry.
The core competencies of the Düsseldorf-based German unit lie in engineering, procurement, construction and related activities pertaining to onshore pipeline systems, underground gas storage, refineries and chemical/petrochemical plants. Its geographical spread includes German-speaking territories as well as locations in which German companies are operational, with its clients including the oil majors and large gas and water utility companies, among others.
A significant proportion of its activities are centred around engineering and construction on large-scale projects, and safety has therefore always been a primary concern for Technip Germany. As such, it is engaged with the roll-out of its Pulse health and safety programme, which is designed to serve not only its own safety needs, but also those of its clients and other parties concerned.
Pulse is Technip’s HSE climate change and performance improvement programme that is used group-wide. Based on industry best practice and research, it has four fundamental aims: that all Technip projects are performed with responsibility for health, safety and the environment; that everyone working on Technip projects embraces HSE as a core value; that the company’s behaviours demonstrate that HSE is a core value; and that Technip is the industry reference company for HSE.
This last ambition is well on its way to becoming a reality for Technip Germany. Pulse was launched internally at first; but was soon transferred to the company’s clients and subcontractors. “Full commitment starts with the company’s management, going down to the very last employee in our company,” explains Sahin. “Education and training takes place regularly and cascades from the top down. It is something we are very proud of developing—it has now reached a status where having trained our employees, the next step is on-site training, including our subcontractors and the client’s management team, in order to share the importance of this value.”
Happily, the success of Pulse is now playing out in Technip’s sites across the world; andTechnip Germany is no exception. It chalked up a notable achievement during the construction of a new hydro-desulphurisation unit within an existing refinery for an oil major in Spergau, Germany—over the course of more than 500,000 working hours, no accidents were recorded.
During peak periods, there were up to 300 people from various European countries on the construction site, with a number of different languages being spoken. Crane activities were carried out alongside other construction work at ground level; and a multitude of different technical tasks were being executed simultaneously. However, in keeping with procedures as laid out by Pulse, no money or effort was spared to ensure that all operations were safe at all times.
A significant investment was made in training of personnel and in the safety and security of the construction works, with the close cooperation of safety engineers employed by Technip and the plant owner on-site. Permanent controls, practice-orientated action plans, regular training courses for personnel and training in the plant were also carried out. These pre-emptive measures resulted in an irrefutable success, with no accidents being recorded throughout the duration of the project; added to which, the work was completed on time and under budget, prompting excellent feedback from the client—the best advertisement for any business.
Indeed, Technip Germany’s dedication to exceeding expectations extends to all facets of its operations. It is currently concluding a project that will increase the throughput of theFujairah Water Transmission System in the United Arab Emirates from 454,600 to 1,045,600 cubic metres per day, with handover scheduled for the middle of the year. The project has been large-scale, involving pipes of 64 inches in diameter—big enough to walk through—lined with cement mortar. Although Technip Germany did not carry out the construction work itself, project management, engineering and procurement fell within its remit and when the supplier of the pipeline’s stainless steel pumps—built to a unique design and the largest of their kind in the world—encountered a delay due to manufacturing failures, it took definitive action. “We recovered the time lost by chartering one of the Antonov aircraft, as we had to keep on schedule for our client,” explains Sahin. The company paid to fly three pumps from Brazil straight to Fujairah airport in Abu Dhabi, rather than risk delay and inconvenience to the client, and successfully recovered the time lost.
Technip has undoubtedly mastered the art of monitoring what matters to its clients, as well as to the industry as a whole. By doing so, it is able to dedicate resource to areas of business growth, and to capitalise on these. For instance, the underground gas storage (UGS) side of its Düsseldorf operations has experienced a boom of late. “For a long time, UGS was not the natural focus of our customers but it is now, and I guess it will remain so—at least for the next six or seven years while more storage capacity (which is definitely needed in Europe), is built,” affirms Sahin.
The energy companies have long since recognised the strategic importance of UGS, and as such, joint ventures in this area of operations are becoming increasingly common. In 2009, Technip Germany commenced services for three UGS projects, one of them in Schönkirchen, Austria and the other two in Etzel, Germany, serving two independent joint ventures on an ‘open book’ basis. This means that a task force comprising staff members from both Technip and the client has been stationed in Technip’s Düsseldorf offices to collectively develop the engineering, order equipment and place construction contracts. With this stage of the project now more or less complete, activity has started shifting onto site, with the entire plant, including running of acceptance tests and performance tests, expected to be finished in 2011.
The success of these complex and demanding projects rests on the dedication of Technip staff—an area which Technip Germany recognises as one of its core strengths. “We have one of the best retention rates—over the last three to four years staff turnover has been at a rate of below three per cent, which is excellent in the market,” says Sahin. “We do a lot to motivate our people.” This includes continuous training and the opportunity for staff to volunteer their expertise to different areas, either geographically or in terms of working discipline, of the Technip Group worldwide. “That gives people reassurance. Technip’s HR programme provides a wide range of opportunities to employees who wish to follow their career aspirations through functional, geographical or cross-segment changes within the Technip Group,” Sahin explains.
Looking forward, the company is actively involved in R&D activities to prepare it for the industry’s growing inclination towards renewables. “Without neglecting our traditional business in onshore pipeline systems, underground gas storage and calcining plants, we are involved in developing technologies to support our clients in regards to renewable energy. Clean energy as an area of focus will be growing, not only within Europe but outside of it as well. Carbon capture and storage; technologies in CO2 compression and transport; efficient reduction of emissions; solar and wind farms; as well as green energy will all definitely be areas of growth,” he concludes.
Editorial research by Vincent Kielty