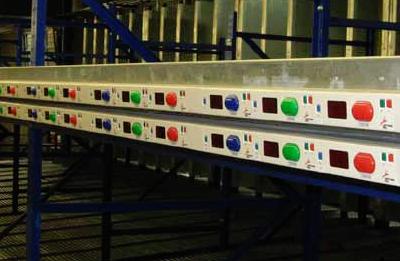
Thomas R. Cutler outlines the advantages of simultaneous picking strategies in light-directed order fulfillment: pick-to-light, pick-to-display, and now build-to-light.
Right now, hundreds of thousands of pick-to-light modules are illuminating in distribution centers across the globe, directing order fulfillment operators to their next correct pick. For over three decades companies have been efficiently processing millions of orders each year with single or multiple light-directed applications in their supply chains. These original installations provided considerable increases in productivity, accuracy and customer service over manual order selection techniques. These legacy pick-to-light applications are also keeping their users from the current best practices and techniques.
There have been many breakthroughs in light-directed order fulfillment technologies, and today’s highly sophisticated systems are quite differentiated from their legacy counterparts. These new solutions offer cable-free light module hardware for greater ease in system installation, expansion, re-slotting and maintenance. They also feature progressive software tools for better management of light-directed picking operations and improved visibility into the productivity of their pick process.
A significant key advance is the application of pick-to-display technologies to support simultaneous order picking strategies, as opposed to the sequential approach executed by pick-to-light systems.
Lightning Pick Technologies has helped numerous companies progress from sequential order picking methodologies to simultaneous pick processes by retrofitting pick-to-light systems with advanced pick-to-display solutions over the past quarter century. According to Bernie McCabe, a senior executive with Lightning Pick, “We have collected data from many of these projects to effectively compare the productivity and accuracy of the two approaches.” McCabe outlines below the benefits of simultaneous order picking and provided case studies of two recent adopters of pick-to-display solutions over their previous pick-to-light systems and the benefits quickly achieved after making the transition.
Over the years ‘pick-to-light’ has become the generic industry term encompassing all light-directed order selection and sortation systems, differentiating the overall approach from paper-based picking, RF picking, voice-directed picking and other methods. Even users of put-to-light for direct-to-consumer fulfillment or retail store replenishment operations (sometimes called pack-to-light) often recognize themselves as ultimately being part of the pick-to-light universe.
However, on an application level there is a vast difference between pick-to-light systems, popular in the first major wave of light-directed systems installed in the 1980s, and the pick-to-display solutions available today.
Pick-to-light
Light-directed systems are frequently applied in zone picking formats to optimize broken case quantity order fulfillment. In zone picking orders travel along an assembly line, stopping at individual pick zones where operators ‘build’ the order by adding items to the order required within their zone. In pick-to-light, a light module is applied to the flow rack, shelving or other storage media at each product location. Each light module has an indicator light to attract the attention of the operator, and a button to be pushed when the picks at that location are complete. Some new light module designs feature indicator LEDs that are also the confirm button.
A bay display (sometimes called a bay controller or bay light) is also applied to each zone, often in a central location in the bay or area. In a pick-to-light environment, often the operator will scan a bar code license plate on the tote or shipping container to launch the pick sequence in their zone. This illuminates an LED at the first product location requiring picks. The operator reads the bay display, which communicates the quantity of those items required for the order. The operator picks that quantity at the illuminated location, and then pushes a confirmation button to complete the pick. After that pick is done, the next LED will illuminate and the bay display will show the quantity needed at that product location. The process repeats itself until all the picks for that zone are complete. The bay display will then direct the operator to send the container to the next zone, or provide other instructions.
Pick-to-display
Pick-to-display takes these benefits to the next level by applying light modules featuring both LED indicators and quantity displays at each product location. When an operator scans a tote in their zone, all product locations requiring picks in the zone illuminate. The operator can see all product locations needed for the order, and each location light module tells them the quantity of items to pick.
Sequential vs. simultaneous picking
Pick-to-light is a sequential pick process. In pick-to-light systems the light modules direct the operator to one pick face at a time. This sequential process makes the operator physically pause in between each pick while waiting for the system to provide the next location. Once the next light is found, the operator must again pause to view the pick quantity presented separately on the bay display.
Pick-to-display is a simultaneous pick process. In pick-to-display systems the operator sees all pick faces needed for the order at the same time. All location and quantity information for the first pick is right in front of her. She can also see that her next hand movement will be to the product location above her current task. After she places items in the tote and turns back to the flow rack, she already knows exactly where her next pick will be. The bay display at her upper right hand side also shares the order number for the job she is working on.
The simultaneous pick-to-display approach is significantly more productive than sequential pick-to-light systems because:
• Pick-to-display removes the pauses between each pick. Simultaneous picking eliminates time wasted waiting for pick directions from the system, allowing the operator to quickly move from one location to the next in one smooth process
• Pick-to-display allows operators to execute one pick while anticipating the next. By seeing all illuminated pick faces at the same time, the operator mentally processes the next pick and prepares for the physical movement necessary for the task
• All the information that the operator needs is right in front of them. This significantly increases pick accuracy and productivity by keeping the operator’s attention in one place—at the actual product location. There’s no need to step away from the pick location to get a better view of the bay display, because the indicator LED and quantity display are both located at the pick face.
• The bay display’s capabilities are expanded. In pick-to-display systems the bay display can share other useful information besides pick quantities. The bay display can present order numbers, lot numbers or special picking instructions to ensure quality and performance.
Bernie McCabe detailed the following two Lightning Pick case studies which highlight the immediate and remarkable results two leading companies achieved when they replaced their existing pick-to-light applications with new light-directed technologies. Among other contributing factors, these users largely attribute the major productivity and accuracy increases to implementing new pick-to-display solutions.
Company #1: A leading manufacturer of personal care products & accessories:
This retail supplier wanted to improve throughput and order accuracy, particularly to optimize its Wal-Mart order fulfillment operation. It replaced its existing pick-to-light system with an approx. 1,600 location system from Lightning Pick Technologies.
The new pick-to-display system installation took 36 hours in total (to completely tear out the existing system and install the new one). Within four weeks of installing Lightning Pick, the retail supplier’s average pick rate of 146 lines per hour (per picker) jumped to 175. This exceeded the initial target rate of 161 lines per picker hour to provide an immediate 20 percent increase in productivity.
During its latest Wal-Mart roll out, the company hit 261.93 LPPH. Since installing a pick-to-display system the customer achieved a 55 percent increase in pick rate productivity. In the four weeks before retrofitting its pick-to-light system, the company averaged a 98.94 percent accuracy rate. In the four weeks after installation, its accuracy rate jumped to 99.35 percent.
All of these goals were met with a 30 percent reduction in labor. The project also improved pick visibility with a newer, brighter light module and pick flexibility was improved by the addition of cordless scanners.
Company #2: One of the world’s leading distributors of Christian resources used a pick-to-light system for its books and literature pick line:
The company wanted to improve customer service by improving the productivity of its order fulfillment process. The new pick-to-display system replaced 1,800 pick-to-light modules.
The new pick-to-display system installation took three days to implement, and was followed by a 22 percent improvement in productivity and a 4 percent increase in order quality. The customer reduced labor costs by 10 percent and was able to fill customer orders the same day it received them. System maintenance and down time costs were also significantly reduced.
Build-to-light
The newest development in these effective supply chain efficiency techniques and tools is build-to-light, used by build-to-order and assemble to order manufacturers. Build-to-light is the first light-directed error-proofing system and reduces errors within critical procedures such as parts picking, kitting, assembly and sequencing among others.
Lights mounted on workstations, bin shelving or other material storage media direct operators to the correct parts, quantities and sequences to execute their task with greater accuracy than paper-based methods. McCabe was enthusiastic about this new product noting, “With increasing demand for customizable manufacturing throughout the supply chain, this new technology is likely to pioneer the next generation of cost-effective picking solutions.”
* * *
Thomas R. Cutler is president & CEO of Fort Lauderdale, Florida-based, TR Cutler, Inc., and founder of the Manufacturing Media Consortium of journalists and editors writing about trends in manufacturing. www.trcutlerinc.com