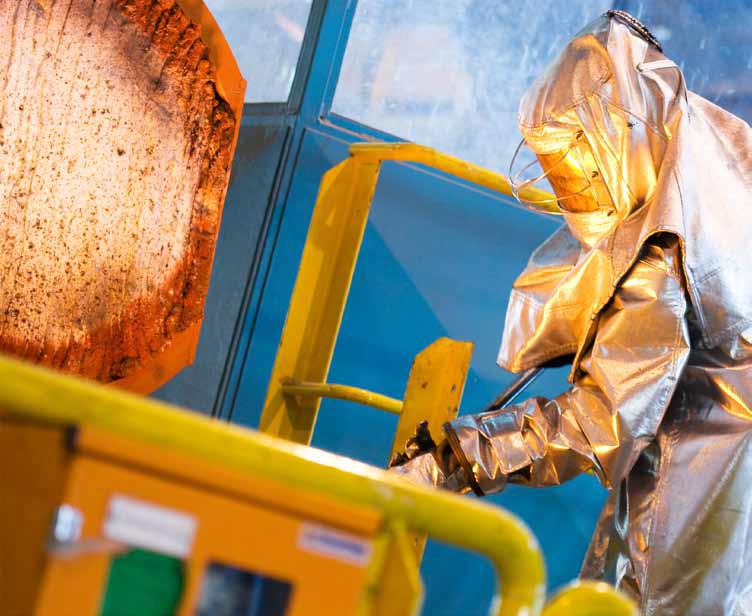
The first new aluminum smelter to be built in the Arabian Gulf in 25 years has become a catalyst for industrial growth in the region, making Oman an attractive destination for multinationals to locate their facilities.
The sultanate of Oman, the eastern-most of the oil-rich GCC (Gulf Cooperation Council) states, is unique in many ways. Perhaps one of the enduring images to capture worldwide public attention in recent months has been that of unrest in the previously stable Arab world. The public response in Oman, though, has been remarkably muted. And this comes as no surprise to Henk Pauw, CEO of Sohar Aluminium. Having joined the company only a year ago, he is able to draw on a vast experience of diverse organizations and cultures. “There is some dissent in Oman,” Pauw comments, “but the government is much more progressive here than in many Arab countries. There are already plenty of plans and initiatives in place to improve living conditions for Omani people. The fact that it maintains good relations with both Palestine and Israel says a lot about its style and modernity.”
These improvements have been funded through a systematic reinvesting of income derived from the country’s oil and gas resources. Alongside its five-year plans, the government has also been working to a 25-year development strategy called Vision 2020 which spans the period 1996 to 2020. One cornerstone of this extensive plan is to reduce dependence on oil revenue by developing a strong national industrial base capable of generating income and jobs.
It was out of this vision that the concept for Sohar Aluminium was born—a project that took three times longer to discuss and plan than it did to build. The economic thinking behind the scheme was based on the ready availability of energy in the form of natural gas, combined with an opportunity to grow a whole range of allied industries and diversify the national economy.
“Aluminum smelting is a process that requires vast amounts of energy,” says Pauw. “At least one third of the cost is for energy, and in Europe that figure would be as high as 40 per cent. So it’s attractive to countries such as Oman, which can convert the energy it has into aluminum production. The gas used could be sold in the normal way but that wouldn’t add value or provide work. The Sohar plant, on the other hand, created jobs for 1,000 people, 70 per cent of them native Omanis.”
Oman’s relationship with Iran is a key ingredient in Sohar Aluminium’s current expansion plans. Cheap natural gas is a great attraction for multinationals to locate manufacturing facilities in Oman, and Sohar Aluminium is but one of several major players that have massive expansion plans, as long as they can secure additional gas supplies. There were hopes earlier this year that Qatar’s Dolphin Energy might provide additional natural gas to Oman to accommodate these expansion plans, but the Qatari government declined that option in May. In June, however, an announcement was made that a deal had been signed for Iran to supply gas to the sultanate through an undersea pipeline by March 2012.
Sohar Aluminium’s ambitious plans to double aluminum output are now very much on the cards. The company was formed as recently as September 2004 through an alliance between three well established businesses, each of them bringing a significant level of expertise and knowledge to the project. Oman Oil, which owns a 40 per cent share in the company, is a commercial body wholly owned by the government of Oman and charged with pursuing investment opportunities in the energy sector, both in Oman and further afield. TAQA, 51 per cent owned by the Abu Dhabi National Energy Company PJSC, another government body, has a further 40 per cent share in the company, and the remaining 20 per cent is provided by Rio Tinto Alcan, the aluminum division of the global mining and metals group, Rio Tinto.
Based on an initial investment of $2.4 billion, the Sohar Aluminium plant is strategically located for easy access to one of the world’s most rapidly growing deep sea ports as well as the region’s rich natural gas reserves.
At the heart of the complex lies a state-of-the-art 1,000MW combined-cycle captive power plant. Equipped with the latest Alstom 13E2 series gas turbine, the plant was designed to meet the stringent requirements of Oman’s environmental agency, MECA, and achieves close to 50 per cent efficiency in converting gas energy into electricity. In addition to this, the site boasts a seawater pumping station that delivers cooling water for steam condensing as well as a desalination facility that supplies the required quality of water to the smelter and power plant sites.
The smelter itself is currently the most modern plant in the world as it was the first smelter to implement Rio Tinto Alcan's benchmark AP36 smelting technology, generally accepted to be the most energy efficient and productive smelting process available. Boasting a single pot line measuring 1.2 kilometers, it has the world's highest known capacity ingot casters capable of operating at 27mt per hour. Meanwhile, the plant features the most innovative elevated walkways, traversing the entire site and keeping man and machinery separate except when absolutely necessary.
The production cycle begins with refined alumina being landed at the plant’s own dedicated port facilities which are operated by Sohar Industrial Port Company, a joint venture between the government of Oman and the Port of Rotterdam. Here, vessels of up to 75,000 tons can berth to offload raw materials and export primary aluminum. As well as bulk materials handling systems there is enough storage space for 120,000 tons of alumina plus 30,000 tons of petroleum coke and liquid pitch—the raw materials needed to make the anodes used in the electrolytic conversion of alumina into aluminum.
After energy, anodes are the largest consumable component of aluminum refining. However, not every smelter has its own anode manufacturing facilities, and the one at Sohar is in itself noteworthy. The Rhodax crusher installed on site is one of the highest capacity machines in the world. Anode manufacturing is an area of the business that Pauw knows intimately, having arrived at Sohar from an anode making concern. “To put the scale of Sohar into context,” he says, “this one plant uses more anodes than my previous business supplied in total.”
With that kind of manufacturing background, Pauw is keen to introduce more modern ideas into Sohar. “We are the most modern plant at the moment,” he says, “but already technology has moved on. We ourselves are considering doubling capacity if we can guarantee energy supply, and when we do, the plant will be designed to AP41. So our current advantages will certainly be short lived. Take out the low cost of energy and our performance is not that productive.”
Starting this year with a small pilot plant in an area he knows will show immediate benefits, Pauw plans to introduce the concept and practice of lean manufacturing. “The Omanis are keen to work and to learn but they don’t have the industrial heritage that exists in the West. Middle management in particular needs a different mindset. We shall be working from the top down so that the momentum will carry everyone along.”
Sohar Aluminium’s pursuit of world class status has already been rewarded in another category, however. In a ceremony held on Monday, 20 June 2011, the company was presented with an award for the “Most Inspired Dashboard” during the Infosol Business Intelligence Seminar (IBIS) conference in Dana Point, California. The dashboard is a graphical tool that has been implemented as part of Sohar Aluminium’s manufacturing execution systems (MES) project, and the award is a remarkable achievement considering the fierce competition from 60 companies worldwide.
Sohar Aluminium’s MES system is used to produce shift reports on production and other key indicators. The dashboard has been designed using Xcelsius software with an easy-to-use graphical interface that provides management with up-to-date information on all aspects of the plant such as production figures, cost, power consumption, local spend and much more. The award is another milestone in the company’s vision to be the best smelter in the world.
Output from the Sohar factory comes in three forms: 27.3kg ingots, 700kg sows and hot metal. Currently, solid metal output at the factory is exported, but the liquid form of aluminum is made available directly to downstream partners located around the plant who then benefit from reduced energy costs in comparison with competitors who have to melt the aluminum ingots or sows prior to processing.
The sultan’s Vision 2020 contains goals for increasing the number of downstream users of locally produced aluminum, and this is being boosted by a global trend in the aluminum industry. The ready availability of oil and natural gas in the GCC states and the resulting supply of low cost energy means the region is rapidly becoming an attractive destination for many high energy industries. And there has been a measurable exodus of aluminum manufacturers away from high cost regions such as North America and Europe.
In 2009 construction began on a new $40 million aluminum rod mill and conductor plant for Oman Aluminium Processing Industries (OAPI), on a site adjacent to the smelter. This was opened in July 2010 and is already running close to capacity using liquid aluminum directly from the smelter. Currently some 50 per cent of the rod mill’s output is in semi-finished wire rods which are exported to the electrical industry in Europe and the other GCC states. The remaining 50 per cent continues through the conductor plant and is converted into electrical transmission cables for the local market.
Meanwhile, the regional market for transmission cable is booming. Driven largely by increased revenues derived from the rising price of oil, many of the GCC states are increasing their levels of investment into power infrastructure. The aluminum industry in the Sohar region is therefore likely to expand considerably over time. There are already further users of the smelter’s liquid aluminum setting up in the vicinity who are likely to come online in the next few years; and OAPI also has expansion plans on the table.
If Sohar Aluminium’s expansion continues as planned, some 600 direct jobs, 1,500 indirect jobs and 7,000 construction jobs will be created, enabling the company to meet its objective of being a major contributor to the national economy and supporter of social development. It already has a considerable track record in this respect, having achieved an impressive 70 per cent Omanization across all levels of the organization and overcoming the difficulties of a largely inexperienced workforce in the field of aluminum smelting.
After just three years in operation Sohar Aluminium has clearly established an enviable reputation for excellence, but continuous improvement is the goal. The comnpany’s development mirrors that of the Sultanate of Oman as it emerges onto the world stage, supporting industrialization and developing the skills and lifestyle of its people. The two are closely linked, and the company’s vision is to become a global benchmark smelter and to play a key role in contributing towards the sustainable development of Oman.