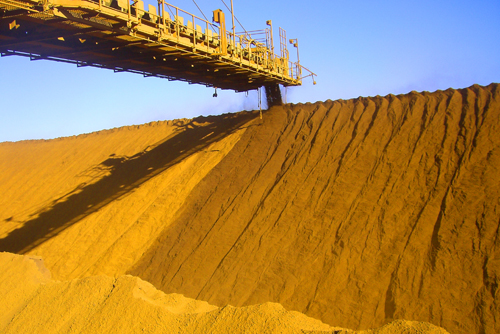
“I think it’s safe to say that business has changed dramatically over the last 18 months,” states Rainstorm Dust Control’s technical sales and marketing manager, Mason Trouchet, when I ask him what life has been like for the Australian company since we last featured them in September 2012.
Headquartered in Maddington, the company, as you may have already gathered, specialises in dust control. Since 1983, Rainstorm has successfully developed and fine-tuned a suite of products designed to stop the large volume of dust created during the various stages of a mining operation from becoming airborne. Whether used on roads, stockpiles, railways, plants or warehouses, its locally-manufactured dust suppression products have proven time and again to increase efficiency, reduce hazards and make processes simpler, cleaner and safer.
“The change in business has come as a result of a number of factors, not least of all the mining booms experienced in key markets including Australia, Colombia, Mongolia and South America, which have resulted in increases in production and thus increases in dust generation,” Trouchet continues. “Meanwhile, attitudes towards environmental responsibility and water conservation have only grown stronger, with the mining community acknowledging that it can’t simply bulldoze through villages and areas and leave them choking on dust.”
Changes within the company and the industry as a whole, over the last year and a half have also come as a result of greater use of connotative data and technologies that are able to quantify the performance of dust suppression products against costs. This has resulted in businesses looking at dust control from a business case point of view, something that was less prevalent in years gone by.
“Dust control covers a number of areas, including roads, transportation, open areas and materials handling,” Trouchet explains. “What the large mining companies are realising now is that there is little point in tackling just one of these areas independently, after all dust you pick off the roads will ultimately just land on open areas and vice versa. So what they are doing now is identifying who can provide a package service that deals with all the aforementioned areas where dust generates and who can do so at the best cost.”
Roads remain the biggest area of interest when it comes to dust control, with studies highlighting that more than 50 percent of all dust generated within a specific project originates from roads and vehicle traffic movements. “Vehicle traffic volumes, particularly in the form of trucks increase during boom periods,” Trouchet points out. “What this means is we have to look at ways to keep the roads pliable, making them moulded rather than stiff and rigid. With increases in road usage customers are also looking for dust control products that are much more performance orientated than ever before. This means applying a solution that stays effective for a matter of months rather than days or weeks.”
The other two main issues of importance come in the form of open areas and materials handling. In the former Rainstorm carries out what it calls veneering, where it sprays a thin coat of solution over stockpiles and open areas. “This process of veneering has been practised for many years, however the interesting development to emerge from this has been the idea of rail car veneering,” Trouchet says. “Recent studies have cast light on the loss of product and amount of dust generated from the use of rail cars by the coal and iron ore sectors, a loss that more often than not exceeds the cost of veneering itself. What we have taken to doing in response is start to veneer the rail cars themselves, thus creating a whole new business positive example of how our technology can not only save our customers cost but also create environmental benefits for the wider community.”
When it comes to the materials handling chain, the biggest topic in recent times for the company has been the issue of dust extension moisture, where moisture is mixed into an ore body to counteract its dusty nature. What Rainstorm has found is that in many instances companies have been using large amounts of water to get the correct moisture content, an action that in itself can cause problems that direct impact upon the productivity of plants, crushing circuits or throughputs.
“By adding certain additives into that water stream to make the material in question less dusty with lower moisture content we also found that we were seeing improvements in throughput and flow, and this in turn was improving things in terms of money gain,” Trouchet enthuses. “So where we were trying to manage dust in the first instance, that was just a cost plus, but the impact we were having on input and flow meant that our customers could in turn increase the capacity of their plants and that has a direct dollar relationship, which meant that these materials created a cost benefit that they didn’t foresee in the first instance.”
The fundamental task of dust control is one that in itself carries environmental benefits, however as Trouchet goes on to tell me, Rainstorm possesses a much more comprehensive attitude towards responsibility and sustainability than just that. “We have always taken a view towards looking at how we can take the by-products or waste materials of other industries and utilise them as a way of supressing dust.”
While boom periods in mining are a blessing to all involved in the industry, it is important to remember that the issue of dust control is constant. Inevitably this means that regardless of market conditions there will always be a demand for the services that Rainstorm provides. Even with that in mind the company still faces a need to evolve and adapt to changes in the marketplace, something that Trouchet appears well aware of.
“When it comes to taking the company forward there are several on-going changes that will determine how we grow and develop. The first is the way our customers are increasingly putting their site-wide dust control contracts out to tender. This is a big shift in approach and is one being seen mostly amongst the larger players in the market. Winning these long-term contracts is of great importance as they allow us to embed our crews and equipment with these customers, and service their needs for extended periods of time.”
The other big change is coming from the development of various technologies that are able to provide detailed breakdowns of where surfaces are being treated, how much product is being used and what the cost benefits of that usage are. “In the case of road treatment, the use of 2D and 3D models is giving us a better detailed cost and performance per square metre overview than ever before,” Trouchet concludes. “This gives us clear data that we can present to potential customers that has been shown to encourage their uptake of our products and services. This is very exciting for us because it essentially means that we are reaching the point where what we have been preaching for the better part of 30 years is now being qualified.”
Written by Will Daynes, research by James Boyle