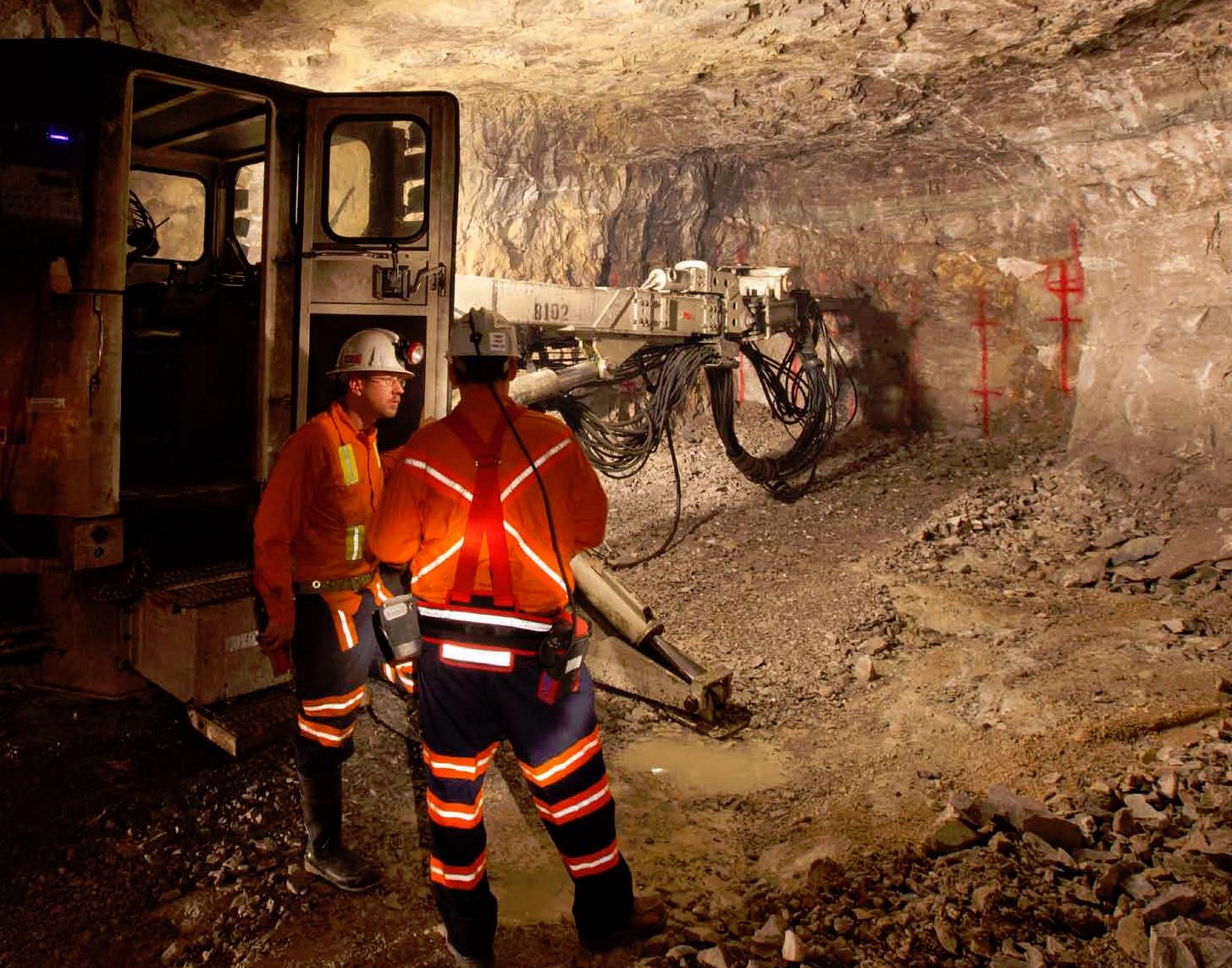
Zinc, one of Nyrstar's primary products, is vital to America's industrial regeneration, and one of the most reliable and highest grade sources comes from its underground mines in Tennessee.
Nyrstar was formed in 2007 by combining the zinc smelting and alloying operations of Australian mining company Zinifex and Umicore, a Belgian materials technology specialist. The combination included a Zinifex zinc refinery located four kilometers southwest of Clarksville. The smelter was built in 1978 to handle the high zinc content, low impurity Tennessee Valley zinc concentrates, something at which it excels – and in any case it is the only primary zinc producer in the United States, with an established reputation as a supplier of quality high grade zinc and alloys.
In 2009, Nyrstar announced its intention to become a mining as well as a processing company, to take advantage of rapidly improving zinc fundamentals resulting from, among other things, economic development in China. It is well known that China is continuing to ramp up steel production to satisfy its massive urbanization projects – and zinc is required to galvanize the structural steel components.
The mid-Tennessee complex of three mines was accordingly acquired in early 2009 as a distressed asset of the former Mid-Tennessee Zinc Corporation. The complex of three mines was in a bad way. “The mine was completely flooded with little infrastructure in place,” says Craig Jetson, now general manager of Nyrstar Tennessee Mines (NTM). A few months later in December 2009 Nyrstar bought from Glencore the East Tennessee complex comprising a further three mines, 250 miles to the east of the Clarksville smelter, and NTM was established.
All six mines are underground operations at a similar depth of some 1,200 feet, though the ore bodies differ considerably in their geology and physical characteristics. They are very much focused on the zinc ore for processing by the Clarksville plant, which now has its entire capacity supplied by NTM.
There are no current plans to increase capacity at Clarksville, he adds, though the smelting plant is currently assessing the business case for extracting a by-product of the ore. Germanium is in demand for optics and electronics, and is found in the ore yielded by Middle Tennessee though not at East Tennessee. NTM is also looking at introducing operational efficiencies, in common with all Nyrstar operations. The commissioning in early 2011 of a new oxide washing facility eliminated the need to import oxide materials and has allowed the smelter to treat local North American sources of material.
If Middle Tennessee has grown from a standing start, East Tennessee has been no less successful in ramping up to full production. Current production rates have been reached in a number of ways and East Tennessee is now producing at a rate beyond any achieved by previous owners, says Jetson. “We have done that through a range of lean production, or de-bottlenecking processes, using a program we call ‘operational excellence’.” Working with the Brazilian consultancy Instituto Aquila, Nyrstar has been able to improve its grades, increase throughput, de-bottleneck its processes and improve its planning and production methodology, he says.
“The result of the operational excellence program has been that in the fourth quarter of 2012 East Tennessee is meeting production rates we had planned for 2013, and there have been significant increases at Middle Tennessee too. We are going to stabilize the business over the next twelve months at those numbers.”
NTM is a single business made up from six separate mines. The mindset of the company, which is global, is to share best practice across all operations. In Tennessee this is put into practice by spreading management responsibility across the six mines with Jetson himself and his safety, HR, finance, mine technical services and engineering managers traveling between sites and only the two operational managers at Mid Tennessee and East Tennessee staying put.
The company's balanced business strategy (BBS) is a five-year rolling strategy that throws out a yearly detailed plan as to how targets are to be reached, using what he describes as 'mining for value' methodology to improve Nyrstar's bottom line. “We are looking at things like equipment reliability, cycling times for equipment, traveling times underground, hoisting times, changes of shift, improvement in capacity of equipment, incremental growth in mining capacity – we also looked at mine plans and mining methods; changing our mining plans significantly to make underground mining more efficient than it was in the past.”
Mining can be sustained from current resources at current rates for at least five years – but in practice it will go on for considerably longer. An aggressive drilling program through the remainder of 2012 and throughout the following year is aimed at extending the resource and upgrading inferred classifications to proven – a revised assessment will be made public in the report and resource statement due to be published at the start of 2013.
Another way of getting the most value out of a mine is 'remote mucking' in which Nyrstar uses fully automated loaders to remove ore that couldn't previously have been safely reached. “We use remotely operated equipment to reclaim ore from areas that were closed down many years ago.” Equipment availability has increased by 22 percent; consumption of everything from tires to explosives and fuels has been optimized, he adds.
When the mines were purchased in 2009 they sustained just 30 employees. Today more than 950 work in them, many of them never having worked in a mine before. The impact on the community in mid-Tennessee has been dramatic – when Nyrstar came on the scene regional unemployment stood at 13.2 percent, now it is about seven percent, less than the national average. But this has placed a burden of training on the company. “We are very proud of our safety performance,” says Jetson. “Some of our mining operations have gone for more than a year without an LTI (lost-time injury) which is an impeccable record in this industry.”
After a long checkered history these mines in Tennessee face some stability at last under the ownership of Nyrstar, which is good news for the employees, too. It is typical of mining that an asset will operate happily when prices are high but go into mothballs when they fall. “We have a good mining plan that we are turning into an efficient and effective production plan. We are managing the business so we can achieve operational value at a range of different zinc prices.” So, a lot less uncertainty for the community and a sustainable business for the longer term. The business is well on track for ISO 14001 accreditation by 2014 – and already supplying ten percent of the nation’s industrial zinc requirement.
Written by John O'Hanlon, research by Dan Finn
DOWNLOAD
Nyrstar-AM-Nov12-bro-s_0.pdf