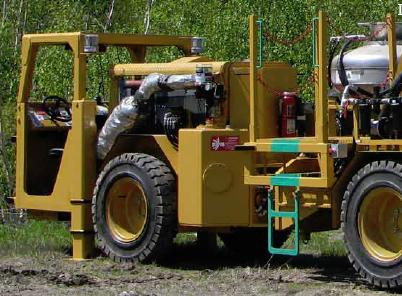
Innovation is part of company DNA at Marcotte Mining Machinery. General manager Denis Rienguette tells Gay Sutton how customization and R&D help the company stay ahead in this volatile industry.
Take the Minejack, the vehicle base upon which most of today’s rugged mining utility vehicles are built, and you’re looking at one of the first innovations from Marcotte Mining Machinery. Started in 1979 as a family business providing services for the mining industry, the company moved swiftly into designing and manufacturing innovative parts and equipment for underground use.
At an early stage of company development, during the early 1980s, Marcotte engineers recognized the capabilities of the Timberjack Skidder—a massive four wheeled tractor vehicle used by the forestry industry to lift and remove entire felled tree trunks—and they saw its potential for underground use. Initially buying-in the Timberjack vehicle bases, the company began modifying them and adding a variety of its own engineered products for use in mine applications. Eventually in 1997 Marcotte became the OEM, taking over the manufacture of the complete vehicle and developing it into a range of sizes and applications.
Today, Marcotte is part of the Timberland Group and employs some 60 people across engineering, sales, manufacturing, and field services, operating from a 35,000 sq ft manufacturing and engineering centre in Sudbury, Ontario. The company specializes in the design and manufacture of a wide range of utility vehicles for underground mining applications, and creativity and flexibility continue to be its driving principles.
“We can customize and modify all our products,” said general manager Denis Rienguette. “After all, our equipment will be asked to perform well under extreme conditions underground, and therefore needs to be adapted to specific mine situations. We have one product in the shop right now—a dry shotcrete sprayer—that is destined for the Kinross Kupolmine in Russia, where the underground temperatures there are typically -15 Celsius throughout the year. Similar conditions occur at the Rio Tinto Diavik diamond mine here in Canada, and we’re working on equipment for that destination too. Meanwhile, we have another wet shotcrete sprayer which we have developed in conjunction with Kinross, which is a self contained unit and holds its own cement. This has goneinto operation in the Buckhorn silver mine in Washington State.”
This flexibility is certainly sought after by the customer, but it imposes constraints on the factory by reducing the volume of standard parts and increasing the incidence of one-offs. Combined with the increased engineering design time, this can add to the cost of the end product. “However, if the customer is procuring, say, ten of these vehicles, the development and production costs are spread across all the products, and we are often able to absorb most of it ourselves.”
In addition to customization the company continues to innovate, developing new products to solve existing issues, and to significantly improve the current range of products. “We must spend something in the region of $0.5 million each year on R&D over and above the amount our customers contribute. Some new products arise from our own ideas, but the majority of them come from customers who approach us with requests for equipment capable of doing something new or different. We then solve that problem for them.”
Marcotte also receives Canadian Government R&D funding through IRAP (Industrial Research Assistance Program), which is granted for specific projects that conform to a strict range of criteria. “We’re currently working on a new design of wet shotcrete sprayer, with money from IRAP for the engineering work. The sprayer solves many of the problems that currently occur in the field, and uses a robotic arm rather than a straight boom.”
Traditional boom-style sprayers have always been prone to damage from rebounding rock or operator generated accidents. The new arm solves this by being highly maneuverable and having fewer vulnerable external parts. Encrustation with cement during operation was also a significant problem as it made it very difficult to grease the old style boom. The hydraulic design of the new arm means it doesn’t require greasing. “As a result, there will be huge savings in downtime and maintenance with this new system,” Rienguette said. “The project is complete now, and we have a number of potential customers bidding for the first one. So now it’s just a waiting game.” Once the bidding is complete the factory will swing into action and the first model will be built within 24 to 28 weeks.
The design of this new product has benefitted from one of the company’s more recent investments—AutoCAD Inventor. Acquired and implemented just two years ago and boasting many sophisticated features, it has revolutionized Marcotte’s engineering and design capabilities. “In this instance, we have been able to apply stress analysis on a variety of places along the robotic boom, and to simulate its use over a period of time,” Rienguette said. The results of the simulations have informed many engineering decisions. “It was a big investment at the time, but it’s certainly turned out to be worthwhile.”
One of the real challenges of operating in the mining industry is it unpredictability. “The market is a rollercoaster, going up and down in cycles with the stock market. It crashed after 9/11 and crashed again during this recession,” Rienguette said. “We have a lot of knowledgeable people in the company who have also been investing in us by remaining with us. And of course I didn’t want to lose any them.”
His strategy to avoid redundancies was to discuss how to reduce expenditure across the company. “We then put the money we saved into building stock equipment so that we could retain our employees during the downturn and we would be ready when things began to pick up,” he explained. “That decision could have gone either way, of course. And we could have been stuck with stock for a very long time. But that hasn’t happened. We’re well on the way to offloading it.”
Now that the global economy is picking up, Rienguette is examining the markets for opportunities for growth. “We’re looking for opportunities to diversity into products and industries that are not affected by mining, to cover ourselves when the industry dips down again. We’re also always looking for new ideas to introduce into the mining industry.” But that is not always easy.
In a competitive market, however, innovation does not remain fresh for very long. “Once a new product is introduced, everybody picks it up and begins to produce it,” says Rienguette. But with innovation built into the fabric of the company, Marcotte is well placed to ride the rollercoaster. http://www.marcotte-inc.on.ca/