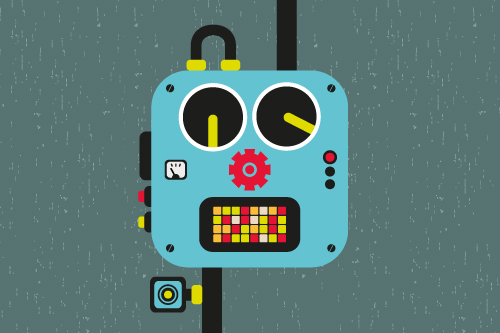
The MTConnect standard facilitates data collection vital for meaningful analysis of machine tool behavior. In 2007, a group at the Association for Manufacturing Technology (AMT) led by Paul Warndorf realized the need for a comprehensive standard to address the inability to collect data from manufacturing equipment. That was six years ago and various machine tool builders and controller manufacturers functioned as islands of automation, requiring proprietary methods to access their data. AMT enlisted the help of the University of California, Berkeley, to develop an open standard making data easily available; this development spurred a new generation of innovation in the manufacturing industry using the latest technologies, including ‘big data’.
William Sobel, presently CEO at System Insights, was a visiting lecturer and researcher at the RADLAB back in 2007 and was asked to develop the standard. Sobel enlisted the assistance of Athulan Vijayaraghavan, who was working on his doctorate in mechanical engineering. Sobel architected and wrote the MTConnect standard with the goal of reducing the complexity and cost of shopfloor data collection and providing a common language for all manufacturing equipment.
Moving beyond OEE
For the past five years manufacturing plant managers and supervisors have adopted lean manufacturing principles, eliminated waste, and still seen total production efficiency elude them. Monitoring and overall equipment effectiveness (OEE) solutions in the shop extracted little value because most ‘OEE monitoring’ technology uses tools that generate data, but none that help them make sense of it. OEE is an effective metric to given an overall sense of how effectively manufacturing equipment is performing; it is not particularly useful in improving shopfloor productivity.
OEE is a composite metric, combining machine availability, part quality, and schedule adherence. At best, OEE conflates each of these individual aspects of productivity, and at worst, OEE incorrectly inflates a device’s productivity by one of the three metrics, overwhelming the others. OEE-based monitoring tools have also emphasized data collection and reporting, aggregating OEE and its constituent metrics from a variety of shopfloor devices and presenting it to users in the form of dashboard and reports. While these applications present valuable shopfloor statistics, they do not offer more than a rearview mirror-view into the shop’s performance.
OEE-based monitoring solutions are reactive; they do not help operations managers understand why devices have low productivity and what opportunities a plant has to increase productivity. Moving beyond OEE, data is needed that can allow a better understanding of what opportunities are available to increase device productivity.
MTConnect and big data
An innovative combination of MTConnect and Big Data technology led to the first significant manufacturing analytic software; it debuted in 2008 at the International Manufacturing Technology Show (IMTS). Sobel and Vijayaraghavan saw the need for applications that went beyond current state-of-the-art capabilities in OEE-based monitoring, and founded System Insights in Berkeley, California. The result was the development of the revolutionary vimana platform for manufacturing intelligence and Big Data analytics.
Sobel had been working with researchers applying machine learning and Big Data analytics in order to make data centers more efficient. The vimana platform is a synthesis of the technologies that are used to enhance the efficiency of financial systems, data centers, and social media. Dr. Vijayaraghavan brought his knowledge of decision tools for designing manufacturing processes and systems, developed during his doctoral work under Professor David Dornfeld at the Laboratory for Manufacturing and Sustainability at UC Berkeley.
vimana
vimana is a next generation software platform with real-time pattern matching and historical machine learning capabilities which makes sense of data from multiple shopfloor sources using the MTConnect standard. Manufacturers apply these data in helping users understand the opportunities to improve productivity. This information is presented in the form of dashboards, real-time metrics, alerts, and contextual reports. Sobel is passionate noting that, “vimana delivers real, measurable value within weeks of deployment by allowing manufacturers to make decisions and understand why machines are doing what they are doing, and not merely what they are doing.”
Traditional OEE-based applications act as data historians collecting data from the machine tools and providing reports. The reports do not add context to what the machines are doing, they merely report the machines’ activities.
Understanding downtime
A key capability of vimana is the auto-classification of downtime in machine tools and manufacturing devices. vimana maps the patterns in the MTConnect data sources in the device including the reason the device is down. vimana can study real-time data from the device leading up to a downtime; it will reveal that the device is down because of a broken tool, or that the device is down for the operator to edit the program to change an offset.
Dr. Vijayaraghavan noted, “These downtimes can then be linked in turn to further activities in the device. The operator’s offset change can be associated with poor part quality or excessive vibration or tool chatter during machining. This capability goes well beyond OEE monitoring, and allows the user to take targeted actions to improve productivity based on the downtime reasons.”
vimana is a powerful data mining engine on the backend which finds hidden trends in the data, like the actual part handling time, the actual cycle times to make a part, the variation in the overrides during producing, differences between planned and actual process parameters. These capabilities help build more insight into the production process and make sustainable changes for the future. In this way vimana makes Total Production Efficiency a reality for the manufacturing shopfloor.
Total Production Efficiency
The capabilities of vimana are delivered to the manufacturing customer using a customer value framework (CVF) model. Based on extensive user feedback, System Insights developed an engagement model unique for the manufacturing industry ensuring that each manufacturer is extracting maximum value from vimana’s capabilities. vimana is first applied in defining a baseline of the plant’s productivity and device utilization. Following this initial process, vimana is used in identifying opportunities for improvement, and as the improvements are implemented, effectiveness is measured using vimana.
Execution of this framework has proven to deliver significant economic benefits to manufacturers regardless of the current state of their business cycle. For expanding businesses, the increased capacity derived by deploying vimana in a CVF engagement model is applied toward growth targets, avoiding new capital expenditures that would otherwise be required to meet expansion goals. Companies applying this new capacity against backlog realize increased profits. Businesses simply looking to reduce cost can eliminate equipment and labor expenses.
By combining MTConnect and Big Data technology, Sobel and Vijayaraghavan pioneered an innovative and industry-first software solution and engagement model for Total Production Efficiency. Aptly named System Insights, these pioneers overcame the limitations of OEE by delivering significant economic benefits to the discrete manufacturing industry in all phases of a companies’ business cycle.