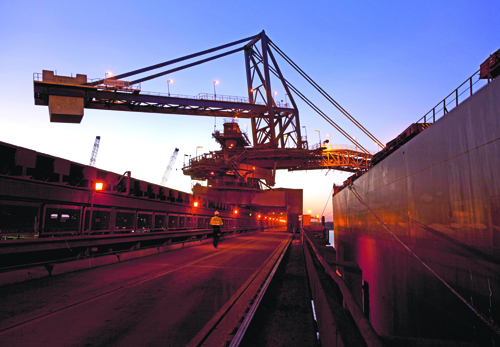
I think it is fair to say that Julie Shuttleworth recognises a great mining development when she sees one. For 13 years Shuttleworth was a part of Barrick Gold, working at various sites in Tanzania and at its Granny Smith mine in Western Australia where, in her role as general manager, she led a team of around 700 people. It was during her tenure at Granny Smith that she would also earn a number of industry accolades, including the title of Australian Mining mine manager of the year in September 2011 and being named among the top ten influential women in mining.
“Having achieved a great deal during my time with Barrick, I reached a point where I wanted to look for a new challenge when it came to my own career development,” Shuttleworth tells me. “Fundamentally I was looking for an opportunity whereby I could be general manager of a larger mine site, and preferably one located in Western Australia.”
Bearing the aforementioned criteria in mind, the opportunity to take on the role of general manager at Fortescue Metals Group’s Cloudbreak mine, located 89 kilometres west-south-west of Nullagine in the Pilbara region of Western Australia couldn’t be more tailored made for Shuttleworth if it tried. It was with this opportunity on the table that she joined Fortescue Metals Group in October 2013.
Cloudbreak was Fortescue’s first mine site, making its first iron ore shipment in May 2008. With a workforce of approximately 2,000 employees and around 1,000 contractors, the mine today processes some 40 million tonnes of iron ore per annum. This ore is prepared and refined within the screening, crushing and desand plants based at the Cloudbreak ore processing facility before being stockpiled ahead of transport to port. Meanwhile the site’s train load out facility feeds up to 16,000 tonnes of ore per hour onto 2.7 kilometre long trains that make the journey along a custom built railway to unloading facilities based at Herb Elliot Port in Port Hedland.
“My first impressions of Cloudbreak were very positive indeed,” Shuttleworth continues. “The first thing that strikes you is the highly positive energy around the place and the go-getting attitude. There is a major emphasis on team work, with everyone from all levels of the workforce keen to help one another. Fortescue as a business has always possessed a strong set of values based on concepts such as family, enthusiasm and empowerment, and those are clearly present at Cloudbreak.”
Coming into the fold as general manager at an operating mine was always going to be a challenge in itself, with the most important thing being to hit the ground running and get up to speed with things as soon as possible. Therefore it was all the more important that Shuttleworth came into her first day in the job with a clear set of objectives for the mine.
“One of the main objectives I have is to drive continuous improvement forward in the area of safety and health across the mine site,” she states. “That is a fundamental requirement for any general manager and I am working constantly with the whole Cloudbreak team, including leadership and safety representatives, to implement greater improvement across the business. The other area of focus for myself is the production side of the mine, particularly working with the processing department to optimise throughput of Cloudbreak’s ore processing facility, while also handling a number of other important ongoing areas such as managing costs and so forth.”
This is certainly a good time to be a part of the Fortescue family. In the last five years the group has undertaken a massive ramp up program, bringing online several other mines and thus increasingly the group’s total production volumes. This in itself is a huge achievement given the dip in price iron ore suffered in 2012. Despite the pressure this created Fortescue’s ongoing success once again highlighted that a flexible and adaptable business will invariably be able to weather challenging times.
Fortescue also holds the distinction of being one of the biggest supporters of Aboriginals in Australia, leading the way in the employment of Aboriginal people and the contracting of Aboriginal run companies. Two months prior to Shuttleworth joining the business, in August 2013, Fortescue announced that it has reached its target of awarding $1 billion in contracts and sub contracts to Aboriginal businesses by the end of 2013, a target that had been set in 2011 and was achieved six months ahead of schedule.
In the months since Shuttleworth entered the general manager’s office at Cloudbreak these efforts have continued with January 2014 seeing Fortescue reach the $1.5 billion milestone, a feat it achieved by awarding a further 145 subcontracts to Aboriginal businesses.
“Fortescue recognises the importance and great benefits gained from employing Aboriginal people and subcontracting work out to their businesses,” Shuttleworth enthuses, “ Fortescue has always believed in the benefits of having a diversified workforce, one made of up of men and women who can bring different backgrounds, experience and ideas to the table.”
At the end of January 2014, 525 employees of Fortescue were Aboriginal, 13 percent of its total workforce, while a further 450 were employed by contractors. More than 250 of Fortescue’s Aboriginal employees living in the Pilbara region also receive housing assistance.
Since 2006, Fortescue has had in place a Vocational Training and Employment Centre (VTEC) in South Hedland and established a second centre in Roebourne in 2010. Together, they have assisted more than 1,000 people. Fortescue’s VTECs aim to break down employment barriers for Aboriginal people, identifying job opportunities within Fortescue and its contractors, and then developing courses in partnership with various training organisations to equip people with the right skills. All successful graduates from the program are guaranteed a job. An average of 150 – 200 Aboriginal people graduate from Fortescue’s VTECs every year, the vast majority of whom are local Traditional Owners.
Environmental awareness is another big theme within the group, understandably given the remote nature of its operations. As well as having reclamation and waste material programs in place, arguably the most important area of importance at Cloudbreak comes in the form of water management.
“When mining a resource like Cloudbreak one of the things you need to do is pump out the groundwater within and around a pit before you can mine it,” Shuttleworth says. “Rather than this water being lost, we transfer the pumped out groundwater into a nearby aquifer downstream from the mine itself.
Fortescue’s managed aquifer recharge system is called Papa Warringka, which is Nyiyaparli for ‘water in the ground’ has been operational since 2008 at Cloudbreak and since 2011 at the neighbouring Christmas Creek site. As well as conserving valuable brackish water it also helps to mitigate environmental impacts associated with surface discharge and groundwater level drawdown. Such has been its success that the innovation was awarded with the International Water Association’s prestigious Global Innovation Award for Water Management and Infrastructure.
Turning back to Shuttleworth, I ask her what her goals are for the rest of 2014 and beyond. The response is instant and shows a clear strategy in place that will help shape the immediate future for the Cloudbreak mine.
“In addition to ensuring we continually improve our safety performance and field leadership within our workforce, I also want this to be the year we increase throughput and reliability of the ore processing facility, reduce our operating costs through various initiatives and increase our own Aboriginal work force from 200 to 300 individuals,” she concludes. “From a longer term perspective it is about looking at optimising grades of material we send to ore and reduce what we send to waste. In doing so we will not only increase efficiencies across the business, but ultimately extend the life of mine as well.”
Written by Will Daynes, research by Jeff Abbott