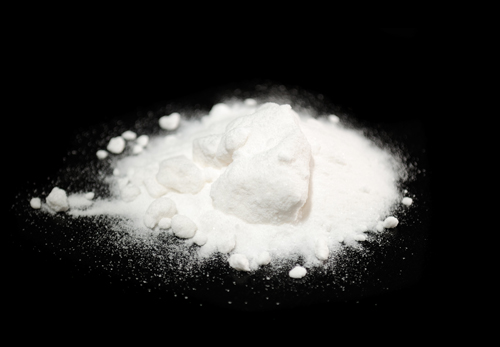
Soda ash is perhaps better known as sodium bicarbonate, and it is a substance with a very large number of applications and uses. Far from being just an antacid that one can take to counteract dyspepsia after a night out, it can be used as a regular food additive, giving sherbet its fizz and noodles their texture. It is also used in baking, photography, as a degreaser, a water softener or a fixative for dyes.
In fact soda ash is almost as versatile and has been almost as much sought after since the earliest recorded history of humankind as its close chemical cousin, salt. Sodium carbonate is a natural water softener, which makes it a common additive to detergents. Products used for these purposes are often sold as washing ash or washing soda. Soda ash prevents hard water from bonding with the detergent, allowing it to be distributed more evenly during the washing cycle. Additionally, the compound has demonstrated its ability to help remove build-up. It can help remove alcohol and grease stains from clothing, as well as calcium build up in everything from coffee pots to hot water boilers. Running a solution of sodium carbonate and water through these systems from time to time will help prevent build up from happening in the first place.
These days there is enormous industrial demand for soda ash. The largest consumer of sodium bicarbonate as a raw material is the glassmaking industry, which depends on it for the greater part of global production. Most glass is soda-lime glass. It is made from silica combined with soda ash and lime. The soda ash lowers the temperature at which the mixture melts and reduces the mixture's viscosity; the lime makes the glass insoluble.
Though the traditional way to obtain soda ash used to be by burning vegetable matter and extracting the mineral from the ash, the only way to supply the demands of major industries like glassmaking, chemicals, photography, detergents, textiles, paper making and water purification was to exploit naturally occurring resources. Though 65 percent of world supply is still produced synthetically natural soda ash gives a cheaper and more dependable product and the proportion is rapidly shifting in its favour.
Soda ash occurs in an ore known as trona, which occurs in only a few places in the world, notably in California and Wyoming. However there are very large trona deposits in Turkey. The Beypazari trona deposit was discovered during coal exploration studies conducted by MTA in 1979. It constitutes the second largest reserve in the world, along with the reserves at Kazan. Both deposits are close to the capital city Ankara. In 1998 ET─░ Soda A.┼×. was established to extract the trona ore and operate the mine to the benefit the economy of the country.
ETI Soda is held jointly by Ciner Energy and Mining, which holds a 70 percent interest, and the Turkish government. Ciner is a diverse industrial group with interests in media and film production as well as minerals. The end product of Beypazari trona ore is ‘heavy soda ash’, which is the product favoured by the glass industry. A series of refining steps are required to produce soda ash from trona ore. First the raw ore from the mine is crushed and screened. The material is then fed to rotary calciners and heated. In this process, the trona decomposes to form crude soda ash, which is dissolved in water. The insoluble shales are separated from the solution by a combination of settling and filtration steps, and the resulting insoluble tailings are taken back into the mine as backfill. The soda ash solution is treated to remove organic materials yielding a high-purity saturated solution of sodium carbonate.
Then the solution is fed to crystallizers where water is evaporated and sodium carbonate monohydrate crystals are formed. The familiar industry term ‘mono-process’ originates from this step. The crystals are dewatered and washed using cyclones and centrifuges, and the solution is recycled to the evaporator units for further recovery of soda ash. The monohydrate crystals are fed to rotary kilns where they are dried to finished soda ash. Finally, the end product is screened and sent to storage silos awaiting rail and distribution by truck.
The ETI Soda plant at Beypazari, built at a cost of $375 million and employing 1,000 people, was commissioned in March 2009 with an opening ceremony attended by Prime Minister Tayyip Erdo─ƒan and the Minister of Energy and Natural Resources, Hilmi Güler. One million tons of soda ash and 100,000 tons of food grade sodium bicarbonate are produced per year, with 90 percent of total output being exported.
The plant was of strategic importance to the Turkish economy. As Erdo─ƒan explained: “We went into action and overcame the technical and financial problems. We focused on this project in 2004 and decided it would brings Turkish industry up to a higher level. We laid the foundations. We completed the facility quickly. Now, we are bringing it into service. Without doubt, now we are at a very crucial point in terms of mining. I have to state that ETI Mining Operations has put Turkey at the top of the global soda ash sector and we are very grateful for their efforts.”
Plans to increase production of the Beypazari complex by 50 percent, increasing its capacity to 1,600,000 tons per annum are in hand. ETI Soda has exported $1 billion worth of soda ash a year to 53 countries since 2009 and expects the new facility to increase this amount to $1.75 billion per annum. Additionally, Ciner Group has just signed a $1.3 billion agreement with Tianchen Corporation of China to construct a new soda ash and power generation facility at Kazan, just 40 miles from Beypazari. Together these plants will make Ciner the largest natural soda ash producer in the world – finally, said group president Turgay Ciner, a Turkish industrial company will be a global number one!
Written by John O'Hanlon, research by Paul Bradley
DOWNLOAD
ETISoda-Euro.Mining-Mar13-Bro-s.pdf