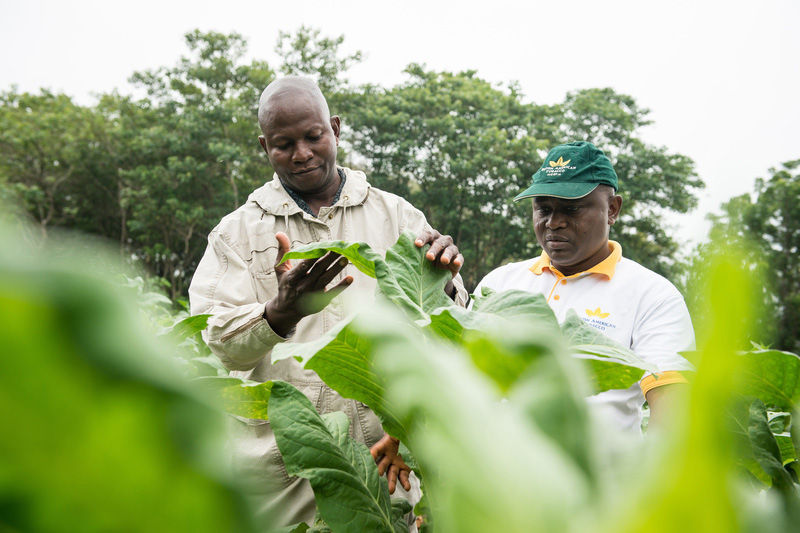
British American Tobacco has never been afraid to embrace change. This is a quality it shares with the most successful businesses throughout history and has been a major contributing factor in the Group’s success over the past 112 years since it was formed in 1902. In recognising the need to move with the times, British American Tobacco has itself evolved into one of the world’s leading tobacco groups, with more than 200 brands sold in over 180 markets, utilising 44 cigarette factories in 39 countries, and a global workforce numbering more than 55,000.
One employee, Bernd Meyer, is as in touch with the concept of change and its importance as any other within British American Tobacco. Meyer successfully transformed South Africa’s Heidelberg cigarette factory from an underperforming operation based on manual labour to a highly automated and high performing state-of-the-art factory. Since then, Meyer has held the position of Global Head of Plan, Logistics and Service for a period of more than a year, and is now almost a year into his current role as Group Head of Supply Chain.
“As you can imagine,” Meyer says, “taking on what was my first global role in 2011 as Global Head of Plan, Logistics and Service involved quite a significant culture change for me, as before my focus was centred on a particular region and area, Southern Africa. What you appreciate first and foremost is the sheer scope of the work at hand. This inevitably means that instead of having a hand in every little detail on an area level, the scale of the global task now requires the need to adopt a matrix management structure of working. This remains the case when it comes to my role as Group Head of Supply Chain.”
One particular cultural and professional change that Meyer would also have soon encountered upon moving into a global role is just how much more challenging it is to put one’s own stamp on things. Fortunately, his recognition of the importance of having a matrix management system in place has helped make this task a little bit easier.
“For this particular department to operate at its best it is absolutely vital that we provide the people who report to us throughout the business with the appropriate levels of direction and focus,” Meyer explains. “This creates a situation where everybody possesses a clear understanding of what our priorities, objectives and targets are as a department, and as a business. This is the first way that one can put his or her marker down and easily spread the message about what you want to achieve now and in the future. This approach also extends to our relationship with our suppliers and in many ways helps to create a strong degree of transparency between all parties.”
Of course implementing change is never easy, particularly within an organisation the size of British American Tobacco. Nevertheless, what Meyer has done in his relatively short time in charge of the Global Supply Chain is identify several areas within the Group that would benefit from a different approach.
The first of these areas is what he refers to as the federalism that continues to exist within British American Tobacco. “We have a situation within the organisation where we have different regions undertaking certain processes in different ways,” Meyer states. “While this can be the right thing to do in some isolated instances, in most cases it proves more efficient to apply the same standards globally, thus creating synergies for the business. One significant example would be having one shared methodology behind how we calculate and determine inventory levels, or on a bigger scale how we apply manufacturing, logistics and procurement processes in our factories and supply chains. This is just two instances among many where I believe bringing agreed processes and solutions into British American Tobacco’s global supply chain can benefit the business both in the short and long term.”
The current implementation of a common SAP system across the world within BAT will finally enable common processes and procedures and also will be a significant milestone when it comes to aggregated, real-time information, faster availability of data and finally additional benefits by avoiding duplication of efforts and having bespoke systems that are not interlinked with each other. This is, Meyer enthuses, a true example of a company and supply chain unlocking the potential of its global scale.
While the primary objective for British American Tobacco’s supply chain, providing value to the business, has remained the same for some time, it has arguably never been more important than today for it to achieve its mission. In a time of global financial uncertainty it has become the goal of the supply chain to achieve savings where possible and in ways that are in no way detrimental to the quality of the Group’s products or the service it provides to its customers and consumers. “In many ways,” Meyer highlights, “the supply chain is increasingly acting as something of a value chain to the business.”
That statement goes some way to encapsulating how the supply chain has evolved in recent times. “I believe that the key to a successful supply chain today is achieving synergy and the best way to do this is through aggregation,” Meyer continues. “The aim of this basically revolves around creating a single drum beat which the department works to, one aligned process if you will, that helps rid the business of the inefficiencies that stem from the multiplication or replication of data and processes. What we have seen in the short time since we began pushing for this model to be embraced is a greater coming together of local and regional supply chains than we have witnessed in the past. Today there are clear signs that a better flow of communication now exits and this has resulted in agreements over shared standards and priorities, things that ultimate benefit everyone concerned.”
Another development that Meyer has witnessed within British American Tobacco has been the way the business rolls out innovations. “We are trying to focus more and more on big ticket items, rolling out big innovations faster at a larger pace,” he highlights. “Instead of trying to invent something in a single end market, what we are doing now involves developing innovations and creating products that we can roll out with speed, while making full use of our global presence. Such an approach didn’t exist in the past, but what it shows is how we are increasingly thinking globally about what is right for the Group.”
While the aforementioned developments have made significant positive impacts on British American Tobacco’s business in their own rights, arguably the most significant evolution to occur within the Group’s supply chain in the last several years has revolved around the concept of having one fully integrated supply chain within the Group rather than having supply chains led by different functions, for instance operations and trade marketing and distribution.
“One of the things we are currently embarking on is the integration of both the primary and secondary supply chains, which have in the past been split into two separate parts,” Meyer says. “While still a work in progress, this supply chain integration programme is now fully in motion and is achieving further synergies throughout the end to end supply chain.”
At the very heart of British American Tobacco is the belief that in order to grow as a business it must operate sustainably, creating value for not only its shareholders, but also society as a whole, and as Meyer is keen to point out, the global supply chain of the Group plays a hugely important role in achieving this aim. “Throughout the world our factories are constantly working on achieving improvements in areas such as energy efficiency, power generation, health and safety, environmental protection and how we can best manage resources, particularly water.”
Furthermore, when it comes to every single investment decision British American Tobacco makes, the Group ensures that it always carries out evaluations in regards to the sustainability of the business. For example, if the Group decides to build a new factory it will first conduct an extensive environmental impact assessment which also considers the long-term impact on the surrounding area of the project in question.
“Long-term thinking has always been a core facet of British American Tobacco,” Meyer enthuses. “The simple fact that we have been around as a business for well over 100 years and plan to be around for well over a hundred more says a lot, in my opinion, about what our thought process is, and without doubt this has influenced the way we look at how our activities influence the world around us.”
As Meyer approaches a year in his role as Global Head of Supply Chain, it seems as good a time as any to ask him what he believes the immediate and long-term future holds for British American Tobacco’s supply chain. Understandably he has several predictions about what will influence his department going forward, the first of those being changing international regulations that target tobacco products.
“Our product’s quality, its taste, has never been more important and has become the biggest differentiator in the market. From a supply chain perspective this puts even more focus on sourcing the best tobacco, the best materials, and developing and producing the best blend that our consumers demand. This attention to detail when it comes to the finished product is one of the main reasons why we stand head and shoulders above our competitors.”
Continued innovation, both in terms of new products released to market and internal processes will also factor heavily on the future efforts of the supply chain. New product categories that gain significant traction amongst consumers, e-cigarettes for example, require almost an entirely unique supply chain in themselves compared to traditional, combustible products, while advances in technology within the Group’s existing infrastructure are helping make vital information more readily available. Quick access to facts and figures covering everything from consumption levels to the use of parts in individual factories is also contributing to faster, more accurate decisions being made at local, regional and global levels.
In many ways this all harks back to that key word, integration. “As a global company it is imperative that we work hard to eliminate inefficiencies at a local level, and the best way to do this in my opinion is for us all to be singing from the same hymn sheet as it were,” Meyer concludes. “Personally, I would very much like it if we were able altogether to stop talking about separate regional and local supply chains, and instead focus on the fact that we have an integrated global supply chain. At the end of the day a company like ours should be one where every man and woman shares the same core objectives and targets, and these centre on providing the best products, made to the highest quality, at the best cost to our consumers.”
Written by Will Daynes, research by Vincent Kielty