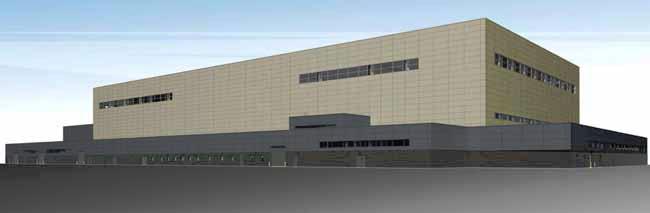
Bird Construction won the largest single-building construction project ever awarded by the Canadian Forces to build a new maintenance hangar for the CC-177 Globemaster III. April Terreri talks to project manager Shawn Stirling.
The construction of Hangar 1 at 8 Wing/Canadian Forces Base Trenton, Ontario, will go down in the history books as the largest single-building construction project ever for the Canadian Forces (CF)—a cost of C$84.7 million. Bird Construction Company of Toronto is the general contractor for this Defence Construction Canada (DCC) project that broke ground in November 2009 and is scheduled for completion in October 2011. It won the contract as a hard-bid project. Bird Construction is no stranger to the Canadian Forces, having built hangars for the Forces prior to this project, such as the Shearwater facility completed last year in Halifax that will house Sikorsky helicopters.
One of the largest and busiest Air Force bases in Canada, 8 Wing/CFB Trenton employs about 3,000 regular and reserve members and over 600 civilian employees. It is a critical hub for air mobility operations and is involved with virtually every CF operation.
The new 250,000-square-foot hangar will be a maintenance building consisting of two bays, each large enough to contain the large cargo carrier CC-177 Globemaster III. The hangar will be 190 meters long by 97 meters wide by 30 meters high. The two bays include a corrosion control bay and a fuel cell bay, reports Shawn Stirling, project manager. A five-ton overhead crane and two telescopic platforms mounted on an overhead rail platform will be installed to facilitate easier access for personnel to work on the planes. The telescoping platforms will drop from the ceiling as required when planes need cleaning and general maintenance.
The building will have two fire suppression systems: a standard sprinkler system as well as a foam system typically used in hangars supporting large planes. “The foam system dispenses a liquid that quickly transforms into a foam that flushes out the fire,” Stirling explains.
The two bays will be separated by a multi-story storage area, and offices, administration and shop support space will line the perimeter on three walls of the building. The fourth wall will contain the two large bay areas, each with fabric doors that will roll up or down on steel supports.
Bird Construction anticipates that 17,500 cubic meters of concrete will be used to construct the footings and 3,000 tons of steel will be used to construct the building. To complete the hangar’s construction, about 2 million worker-hours will be required.
A job of this magnitude certainly comes with its challenges. One challenge is being met currently as the extensive concrete foundation is being constructed. “We’re forming and pouring the foundations right now, and we expect to pour about $2.5 million worth of concrete,” reports Stirling. “We’re pouring very large footings currently; I’ve never poured footings this large before.” He adds that the forms vary in size but that the largest single pour footing so far is 50 meters long by 6 meters wide by 3.5 meters deep. Some of the pours require 800 to 900 cubic meters of concrete. The formwork is being done by Avenue Building Corporation of Bolton, Ontario, a well-known company in the concrete forming business. Stirling explains that the purpose of these massive footings is to prevent any chance of uplift, keeping the building from lifting into the air. The foundation work is scheduled to be complete by late spring, when the structural steel work will begin.
The next big challenge will be the erection of the structural steel. “They will build 12-foot-high trusses on the ground, two at a time,” explains Stirling. “Then they will brace the pair and jack them up to the top of the columns.” This method is a bit different from the traditional method, which uses two cranes to lift the trusses into place. “But the erector on site wanted to try using this jacking method to see if it proves to be a more efficient and time-saving method.” Twelve groups of these pairs of trusses will be required for erecting the structural steel. The shell of the building will be composed of exterior-grade gypsum sheathing, air/vapor barrier, insulation and composite metal paneling.
Because of the size of the building and the magnitude of the various construction components involved, safety is a primary concern, notes Stirling. “Safety has always been a paramount consideration for Bird Construction,” he says. “We make sure that everyone on site has taken a safety orientation seminar so that each person understands the safety measures involved for each project.” Because the construction industry is driven by deadlines, a great deal of diligence is required in order to maintain the discipline necessary to pre-plan and integrate safety into every activity. Stirling notes that every worker on site is assured of a safe environment in which to work.
Stirling credits the project’s successes so far to the strong team relationships between Defence Construction Canada, Bird Construction and its subcontractors. Lead contractors include JMR Electrical of Exeter, Ontario, responsible for about one-third of the project, including the mechanical and electrical work. Overseeing the steel construction and erection is Burnco Manufacturing of Toronto, whose erector is DCM Erectors, also of Toronto. “We have an outstanding team on site with Bruce Stienburg, project superintendent; Steve Williamson, superintendent; Cameron Mitchell, site coordinator; and Ian MacDonald, quality control manager,” says Stirling. “We’ve worked with these men over the years, and they are extremely knowledgeable about our standards and our methods of doing things.”
Bird Construction Company has completed billions of dollars of work as a general contractor during the 90 years it has been operating since first opening its doors in 1920. The company operates nationally and has eight offices from Vancouver to Halifax. It employs about 200 people and reports revenues over C$1 billion.
Stirling notes that the strength of the company has always been to work closely with each client to get the job done according to the client’s expectations. “We have always had a very good relationship with DCC, and the team approach we use on their projects helps us get the job done as efficiently and effectively as possible,” he says.