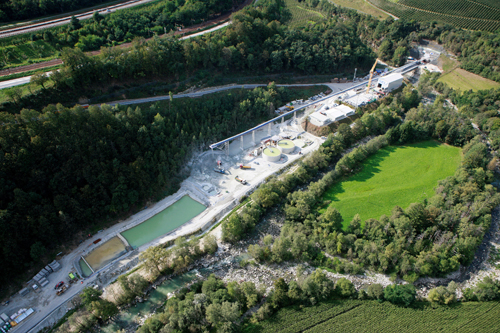
The Alps are Europe’s great natural boundary, cutting Italy off from the rest of the continent. Getting from one side to the other whether for purposes of travel, war or trade has been a headache ever since ‘the iceman’ Ötzi lost his life 5,000 years ago on the Fineilspitze, not 20 miles to the east of the Brenner pass.
The Brenner was not used for regular traffic until the second century AD and remained a very minor crossing right up to the late 18th century when Maria Theresa caused a road to be built. It is however the lowest of the six major Alpine passes, which is why it was chosen as the route for the Brenner Railway from Innsbruck in Austria to Bolzano and Verona in Italy. However the railway still has to climb to fairly dizzying heights, reaching 1,371 metres at its highest point, on the border between Italy and Austria and overcoming the gradient by means of two spiral tunnels. That means it is a slow route, exacerbated by the need to change engines.
Goods traffic between northern and southern Europe is constantly increasing and it is the goal for much of this traffic to be transferred from road to rail to protect the sensitive Alpine environment, which is a global heritage. The case for creating a ‘flat’ rail link, along which more of this freight can travel became compelling as long ago as 1971 when the International Union of Railways (UIC) commissioned a study for a new Brenner railway with a ‘base tunnel’ – a term which is a direct translation of the German ‘Basistunnel.’ By 1989 three feasibility studies had been drawn up which formed the basis for further planning of the Brenner Base Tunnel, however it wasn’t until 2004 that BBT-SE, the Austro-Italian company that is building the tunnel, was formed.
The BBT is much more than just a tunnel through a mountain. The €8.5 billion project, funded by the EU and the Austrian and Italian governments, is the main element of the new Brenner railway from Munich to Verona. It is a key link in the priority EU project to create a 2,200-kilometre railway axis between Berlin in Germany and Palermo in Sicily. Three quarters of this axis is already under construction or actually operational.
The only way to create a high-speed line across the Alps was to tunnel below them: the maximum elevation above sea level is just 794 metres and the steepest incline just 6.7 degrees. The BBT is 55 kilometres long from Fortezza in Italy to Innsbruck North, however if you add it to an existing section built in 1994 that bypasses the city emerging at Tulfes, the tunnel is 64 kilometres in length, making it the longest underground railway connection in the world.
Professor Konrad Bergmeister was appointed CEO of BBT-SE in August 2006 and has led the company ever since. Bergmeister is best known as an academic engineer, with 400 scientific publications to his name. On the faculty of the University of Natural Resources and Applied Life Sciences in Vienna, he has taught construction engineering for the last 20 years, and in addition he has been the President of the Free University in Bolzano since 2010. However he has also acted as the technical director and head engineer of the company managing the Brenner highway.
All that experience has stood him in good stead while negotiating the sometimes labyrinthine progress of the tunnel project. Work on the €403 million first stretches of exploratory tunnel should have started in 2006, but it was two years later in 2008 work actually started. The original target date for the trains to start running through the tunnel was 2020: this has now been extended to 2025, though Bergmeister thinks that this is realistic.
The design and method of construction of the tunnel are both unconventional: the twin 8.1 metre diameter main tunnels, one carrying northbound, the other southbound traffic, are separated by a third six metre ‘exploratory’ tunnel that is being built ahead of the other two. Connecting tunnels link the main tubes ever 330 metres, providing a high level of accessibility-and security.
The exploration tunnel will be valuable as a drainage and service asset (it lies twelve metres below the main tunnels) once the other two have been built using a combination of blasting and tunnel boring, depending on circumstances, though 70 percent will be excavated using TBMs. The main reason for driving a pilot tunnel was a geological one, Bergmeister explains. “Though we know a lot about the geology of the Alps, it was impossible to know exactly what rock conditions we would encounter. The tunnel has to cross something called the periadriatic fault, or seam: we know it is there but at that depth we don’t know exactly how it behaves.”
The exploratory tunnel is important to obtain further information about the inside of the mountain and therefore plan the construction of the main tubes with a higher degree of precision, he emphasises. “Such geological information as we started with was based on preliminary studies that have been going on for decades. More than 34 kilometres of drilling was done, in which over 27,000 cubic metres of stone were removed from the mountain, to evaluate the rock mass along the planned tunnel route.”
During construction the spoil from the main tunnels will be removed through the exploratory tunnel, speeding up the latter stages considerably. “We are removing all the spoil from the main tunnels through the exploratory: it is moved all the way to the discharge site using a series of conveyors and no trucking will be involved,” says Bergmeister. In all there will be 17 million cubic feet of spoil to be disposed of, and this will come out through four access tunnels, of which the ones nearest the Austrian and Italian ends are already complete. The 1.3 kilometre Ampass access tunnel and the 2.4 kilometre Ahrental access, together with about a quarter of the exploratory tunnel on the Austrian side, have been completed. The Wolf access tunnel was the last to be put out for tender for an estimated contract sum of 140 million earlier this year, and is now progressing well. This is also the longest, at four kilometres.
Currently, completion of the exploratory tunnel early in 2014 is a priority. TBMs capable of advancing 30 metres a day stabilise the ground as they go using piles and special grouting, and the tunnel is lined with 20 centimetre thick segments manufactured off site using a steam system that accelerates setting. The cutters mounted on the face of the TBM cut the rock into chips which go into a hopper that drops them onto a conveyor belt at speeds up to 700 cubic metres per hour.
The Brenner Base Tunnel will change the face of Europe’s infrastructure forever, says Konrad Bergmeister. “We have turned to the most innovative technologies and materials in designing this tunnel for a lifetime of more than 200 years!” he says. As a world authority in concrete engineering, his word is to be believed.
Written by John O’Hanlon, research by Abi Abagun
DOWNLOAD
BBTSE-Euro-Const-Jan14-Bro-s_0.pdf