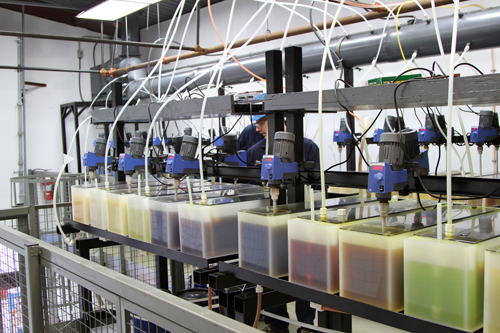
Junior mining companies are feeling the chill these days, and have been under pressure for over a year, so it is heartening to find one whose neat footwork has turned the situation to its advantage. Over the past year Argex has advanced its plan to convert its focus from mining to production of Titanium Dioxide (TiO2), a commodity that is sure to grow in demand as the world emerges from recession, because its sales in any particular market shadow GDP with uncanny accuracy. It is a key ingredient in paint, as well as in many pharmaceuticals, plastics and paper, having unique properties of opacity and whiteness.
Wearing its mining hat, Argex accumulated a portfolio of properties in Quebec that provide it with a source of ilmenite, the ore from which TiO2 is derived. In 2009, it acquired La Blache together with an iron ore project called Mouchelange on the north shore of the St. Lawrence River, and in 2012 added another interesting property called Lac Brûlé. These properties, it was thought, would provide feedstock for a process of beneficiation if a suitable technology could be found to produce high grade TiO2 from ore containing contaminants, or penalty metals as they are known, that are intractable in the traditional processes the industry is used to.
The company accordingly worked in partnership with Process Research Ortech (PRO) to develop a proprietary mineral extraction process that allows for the production of 99.8 percent pure pigment-grade TiO2, which can be sold to the end-users in the paint, plastic and coating industries. The CTL process has significant advantages over current processing methods: it has a very low environmental impact, operates at atmospheric pressure, does not require high temperatures and produces saleable by-products. “The comparative risk-profile for scale up with this technology is really very low,” says Roy Bonnell, Argex Titanium's president and CEO.
The last year has been a busy and a productive one for Argex. The raw material for the process, ilmenite, is readily available and Argex has been exploring the idea of treating commercially available ore bodies in addition to that from its own properties. One of the things that makes Argex different, and endears it to shareholders and analysts alike, is its approach to risk. “Commercial sourcing was attractive because it meant that in starting our plant we wouldn’t have to have two different capital projects going on at the same time. Here in Quebec, developing a mine can be a lengthy process so to be able to have cash flow earlier in the economic model creates a lot of present value for our shareholders.”
Argex Titanium's business model was given additional support in July 2013 when it announced a $10 million private placement with Investissement Québec, and a US-based investment fund manager which already holds Argex shares. “The Quebec government is proud to support this strategic investment project, which will have substantial economic spin-offs for the Montérégie region,” said Québec's Minister for Industrial Policy Élaine Zakaïb. The funds will go towards developing the 235,000 square foot plant it has acquired at Salaberry-de-Valleyfield that will be home to its first full-scale TiO2 plant. And it's not just the money: government support for a project like this, which depends heavily on infrastructure, is crucial, Bonnell says.
Valleyfield is an ideal location, an industrial site already occupied by major chemicals companies that can support Argex's supply chain. It is well served by air, road and shipping links, is close to gas and electricity supplies, and has a pool of experienced workers. “Even the community college is focused on producing chemical technicians,” he enthuses. “We feel we fit in there.” Getting Valleyfield up and running is now a priority. The first step is to move the pilot plant, which has tested the new process on a variety of differing ore bodies, from Mississauga just outside Toronto to the Valleyfield site. This is important because it will mean this vital research facility will be on-site, able to train the people who will be working on the full size plant.
At the same time, the company is working with its engineering partner Genivar on a bankable feasibility study (BFS) that will make the economic case for the plant, as well as outlining the engineering aspects including plant layout, equipment required and workflow. The results of the BFS should be available in September, demonstrating the potential game-changing nature of the CTL process, and placing Argex in a position to evaluate partnership opportunities, engage in detailed construction engineering work and start hiring suppliers. Bring it on, says Roy Bonnell, who wants to see first production in the first quarter of 2015. I am doing my best to hold the engineers' feet to the fire!”
There will always be bumps in the road, but the scalability of the company’s process, compared to many other metallurgical processes, is not particularly difficult. Indeed this was why the company chose to occupy an existing building, already laid out as a chemical facility, rather than build from scratch. It is another risk-reducing factor, he says, not least because you don't want to be waiting for concrete to set in Canada's winter! The process itself is hardly action packed, consisting mainly of leach tanks and settlers: it can be described as – well, boring. But that gladdens his heart. Boring means low risk. “We tested around ten different feedstocks, and found we could use any one of them. One that we have been using and will probably start with is high in only one penalty metal.” Yet another prudent approach – having to deal with just one rather than three or four limits the risk of problems in the startup phase, he says.
By this time in 2015 we expect to be reporting on the plant in production, shipping its high quality product into an expanding market. The market fundamentals are promising, he points out, with the US economy rising out of recession and construction readying itself for activity following a period where projects were put on hold. It will be pigment’s day again and prices are predicted to rise with demand, which as we have noted tracks GDP. An interesting statistic is that annual per capita consumption of TiO2 in the USA is eight pounds: in China and India it is two. The global market for the higher quality CTL product with its outstanding light reflection qualities, as opposed to the lower performance chemical resulting from the sulphate process, will inevitably grow alongside living standards.
In that case, Valleyfield will come on stream just at the right moment. “In the coming year, you will see our further evolution to becoming an emerging producer of a speciality chemical and more an engineering company than a miner.” The R&D centre will be up and running at Valleyfield well ahead of the main plant, which will employ around 100-150 people. It will be a showcase facility, Bonnell says, and a model for other plants Argex might build in the future in locations that have lower energy costs.
However for the time being, his policy of cutting risk to the bone is paying off. Appropriately, at the end of June 2013, the company signed a purchase agreement with the company it has collaborated with since 2011. PPG is the largest paint company in the world, and its confidence not only in the process but in Argex's strategy and ability to deliver is as important as the deal itself. It establishes Argex in the market as a company that is doing real cutting edge work. “We will continue to align ourselves with blue chip companies like that. You are judged by the company you keep, and I think it is important as we establish ourselves that we are seen in alliance with people like PPG.”
Written by John O'Hanlon, research by James Boyle
DOWNLOAD
Argex-AM-Mining-Sep13-Bro-s.pdf