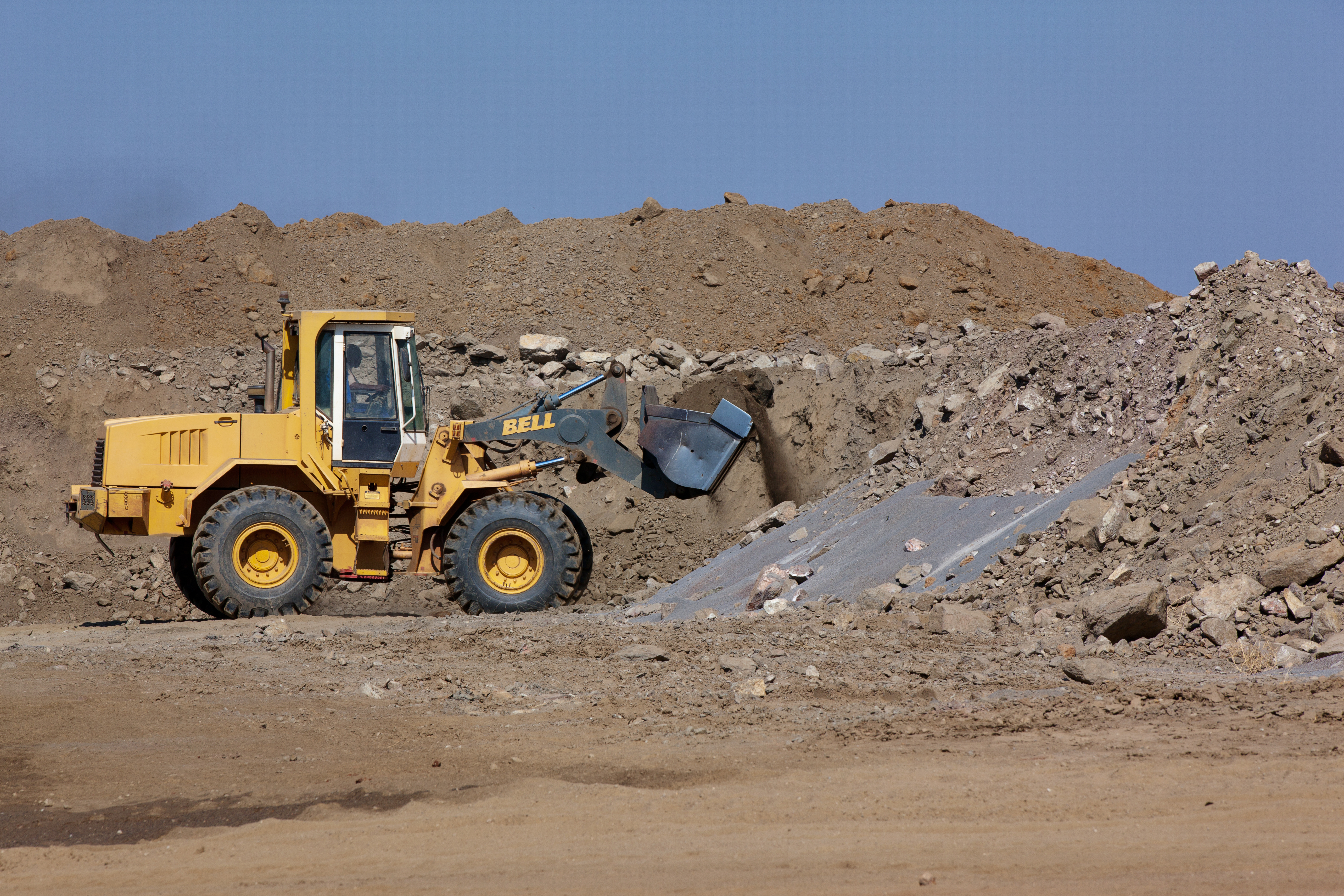
One South African mining company is producing a refractory material on whose properties the world’s iron and steel producers depend.
In the production of iron and steel, refractory materials fall into the category of consumable commodity—hovering somewhere in the background until all the glamorous hard work has been done and the melted, smelted, refined liquid metal needs moving in a refractory lined vessel from one part of the plant to another.
One of the interesting aspects of these heat-resistant materials, though, is the rate at which they are consumed. Japan is the most frugal, requiring on average just six to eight kilos of refractory material per tonne of steel produced. Germany is not far behind with an average of eight to 10 kilos per tonne of steel. China, on the other hand, is much more profligate. There, an average tonne of steel gets through 25 to 30 kilos of refractory.
“There are numerous refractory materials that can be used,” explains Andreas Pabst, sales and marketing director of Andalusite Resources of South Africa, “and once chosen, there is a strong resistance to change. So despite the obvious superiority andalusite demonstrates in Japan and in Europe, in some parts of the world it is a slow process weaning them away from what they know.”
Andalusite, as your Spanish geography might suggest, was first discovered in southern Spain about 150 years ago. Then, though, it was in the form of a gemstone. The South African version has also been known for many years but it doesn’t have the same aesthetic qualities as its Spanish cousin. In fact until the 1970s, there was no known use for it. Until, that is, the Weedon family began its pioneering work of marketing andalusite as a refractory material. Since then, it has been positive—albeit slow—progress to the position it holds today.
“The refractory industry is understandably extremely cautious and conservative,” says Pabst. “Should anything they supply not fulfil its job and the refractory fail to contain its load of white hot liquid metal, the financial penalties could be enormous; the risk of human injury has to be avoided. As such, it is not unusual for it to take up to 18 months for a new refractory to be assessed and approved.”
Andalusite is an ideal refractory material. It has high thermal shock resistance so can take the temperatures and fluctuation found with molten metals and ceramics. It has an ultra-low expansion rate so doesn’t crack; and unlike some materials, it has a high chemical resistance—in other words it does not react with other materials while exposed to the extreme conditions of heat and pressure as reign in ladles and furnaces.
Historically, South Africa’s deposits of andalusite were found in the east of the country, producing a course crystal of up to eight millimetres. In the 1990s, Rhino Minerals began looking in the west and found considerable deposits of a finer grained material. Andalusite Resources’ mine, 220 kilometres north-west of Johannesburg at a place called Maroeloesfontein near the town of Thabazimbi, is adjoining the Rhino leases.
“It’s not a difficult mining operation,” says financial director Colin Bain. “The andalusite is found in decomposed shale and requires no blasting. At its widest, the ore body is 800 metres wide and we are mining open cast down to about 35 metres. The ore body goes much deeper but below this level there are more impurities to contend with that make the extraction uneconomical. Once a further two leases that we are applying for are granted, we will have enough reserves to last a hundred years.”
Four metres of overburden need to be stripped away, leaving the ore to be dug out by two excavators—one of 70 tonnes capacity and another of 20 tonnes. A fleet of 30 tonne trucks ferry the ore just one kilometre to the processing plant. The ore contains around 12 to 14 per cent andalusite and the extraction process is essentially one of crushing, washing and screening.
However, before any of this starts, run-of-mine ore has to be stockpiled separately as the andalusite varies subtly from location to location. Considering that the composition of the finished product is so critical, considerable care is needed at every stage to ensure optimum quality. Stockpiled ore is continuously sampled and blended before going into a feed hopper. Conveyors take the ore through a series of crushers designed to release the andalusite gradually without shattering individual crystals which, at Maroeloesfontein, stop at three millimetres. Although as the mine expands further north, the crystallography becomes coarser, and in the not too distant future Andalusite Resources will be able to offer a coarser grade andalusite too.
At the end of this sequence is a 40 per cent concentrated slurry which, once it has gone through a bank of cyclones, is enriched to 98 per cent. The final part of the process is to magnetically remove any iron particles that remain, after which the product is bagged ready for despatch.
All the andalusite mined is taken by customers in the refractory industry with around 60 per cent going to iron and steel manufacturers. Upwards of a quarter of annual production goes to the local southern Africa market, another 30 to 40 per cent goes to Europe and the balance travels east. Steel makers in Japan have been among Andalusite Resources’ best customers and consistently take around five per cent of production.
“Japan is a very sophisticated market,” says Pabst. “They were among the first to recognise the benefits of using andalusite and have proven very loyal. Chinese and Indian manufacturers, on the other hand, are still more inclined to buy on price and consequently buy something inferior. We have a superior, high quality product but still take a pragmatic view, aware that there is considerable competition within the market. Nevertheless, there is much more we could do in those markets providing we explain the benefits to be had from andalusite.”
Last year production was expanded and could be lifted very quickly from the current 72,000 tonnes per annum to 100,000 tonnes. At the moment, though, Andalusite Resources is in cruise mode and holding back on any increase in output, conscious that there is a trend towards consolidation within an over-supplied iron and steel industry. Instead, the emphasis is on improving quality and developing new products. “We are working closely,” says Pabst, “with German refractory engineers Mine Feuerfest, who are helping us develop new applications which could replace strategically important minerals currently sourced from countries that have a question mark over the reliability of supply.”
Written by Alan Swaby; research by Robert Hodgson
DOWNLOAD
Andalusite-EMEA-July12-Bro-s_0.pdf