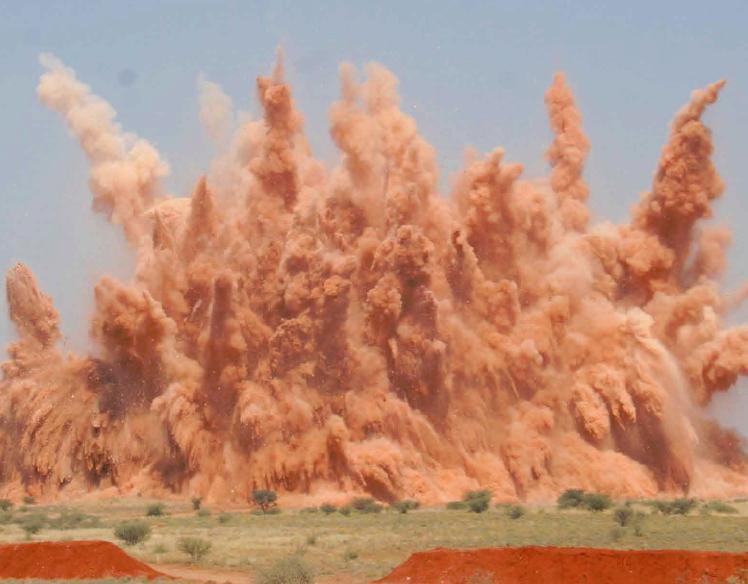
Kudumane Manganese Resources is developing its mining operation in one of South Africa’s poorest regions, and is keeping simplicity and the local community at its core.
South Africa-based Kudumane Manganese Resources is the latest mining operation to enter the competitive manganese ore industry. Located near Hotazel in South Africa’s Northern Cape Province, the mining operation will produce manganese from the rich deposits that characterise the region. The project is located about one kilometre from Hotazel and about 50 kilometres from Kuruman.
Kudumane Manganese Mine is owned by Kudumane Manganese Resources, a joint venture between two BBBEE companies, Dirleton Minerals & Energy and the Northern Cape Manganese Company (NCMC), which own equal shares in the firm. Hong Kong-based manganese multinational Asia Minerals Limited (AML) owns a 49 per cent share in both companies, and is the project’s technical partner. AML will market and sell the manganese globally and has arranged all project financing in its role as technical and marketing provider. Bold Moves and NWC Manganese are also shareholders in NCMC and Dirleton.
The R1.5 billion project will consist of both open pit and underground mining, with the intention of shipping an initial 1.5 million tonnes of manganese ore out by both road and rail to the harbour at Port Elizabeth each year. When the Coega Industrial Development Zone and Deepwater Port becomes operational outside Port Elizabeth, it will become the preferred exit point for the mine’s product. Production of manganese ore from the project is expected to eventually increase to two million tonnes per annum and later 2.5 million tonnes per annum, with the introduction of underground operations in 2019. The expected life of the mine is 10 to 15 years for the open pit or combination mining operations, after which underground mining will continue for an estimated 30 years.
The project infrastructure consists of an open pit or combination open pit and underground mine, a crushing and screening plant, mine residue disposal storage and facilities, and various other support infrastructure and services.
The project will be in full production by end of 2013, with the first phase being bulk sampling activities followed by production. “We are currently at the first stage of the project, which is pursuing bulk sampling,” explains Kudumane Manganese’s project manager Schalk van der Merwe. “That will be complete by December. Then we will be building the rest of the infrastructure, including a railway siding for future loading of the manganese, housing, offices, workshops and stores. We’re just spending money at this stage!”
The infrastructure to be developed as part of the project includes 5.3 kilometres of railway siding, an automated 3,500 tonnes-per-hour rapid loading station, road trucks with a loading capacity of 300 tonnes per hour, a crushing and screening plant, and storage facilities to handle the mine’s residue. Plans are also underway to construct a sintering plant, which will allow the mine to ship out the ore after undergoing this pre-smelting process. Other infrastructure being developed includes roads and general developments in and around Hotazel such as housing, schools, and a hospital.
As the project is located in the remote and harsh environment of the Kalahari Desert, bulk services had to be laid down from scratch at the outset. “That has been our biggest challenge,” admits Van der Merwe, “getting bulk services in such as water and electricity.”
However, despite the challenges, it is the simplicity of the project that defines it, says Van der Merwe. “The operation is a simple set-up with no major technology involved—it is a simple blast-and-haul mining process. The plant itself is also very simple. There’s no technology involved in the first phase: for the next five to seven years, it is a simple process. This keeps the level of capital investment low as well.”
The operation occupies one of the poorest regions in the whole of South Africa, and Kudumane Manganese hopes that its social and labour plan will have a positive impact on surrounding communities. “The social and labour plan makes provision for many different activities we must undertake according to the Mining Charter in South Africa.”
Under the Mining Charter, mines should work together and pool their resources in order to maximise their benefit to an individual area, he explains. “So we’re now negotiating with other mines to see what is already in place; and at the same time we’re talking to local communities to see what is outstanding and what we still need to do.”
The company has recently met with the regional council to identify the activities in which it can participate. The mines in the area are looking at developing Hotazel; as well as the housing, schools and hospital, the mines hope to bring in a better water supply, as the current supply is not sufficient for the population. Also on the agenda is the renovation of electrical power lines. “This is the poorest part of our country, and anything that is of assistance is greatly appreciated by everybody,” says Van der Merwe. “There’s a lot of participation locally and a welcoming environment, ensuring everybody benefits.”
The company also has a robust plan in place to employ local people. “As part of our social and labour plan, 80 per cent of our skilled workers must come from the local community; then we aim to ensure that through skills transfer, 100 per cent of our workers will come from the local community in the future. We will achieve this through giving out bursaries, training, or whatever is needed; but eventually that’s our goal.”
The bulk of workers will be sourced from within the region’s John Taolo Gaetsewe District Municipality. Once fully operational, the project will give preference to the locally unemployed wherever possible, and only where local employees cannot be sourced with the requisite skills and experience will national recruitment take place. Specific areas that will benefit from the employment of between 200 and 300 people directly and up to 300 indirect employees will be the Joe Morolong Local Municipality, the District Management Area, Hotazel as a whole and thereafter the rest of the province. Up to 500 people will be employed during the construction phase.
In terms of the environment, the operation’s simple nature means that risks are fairly easy to assess, says Van der Merwe. “In essence there’s not a lot of waste from our mine. However the biggest risk is fuel: we store a lot of fuel on-site for our equipment, so that’s our biggest environmental risk. The rest is simple, it’s all from the mine—issues such as dust, for example. But there’s no hazardous material from the mine itself.”
The key to success on this project has been keeping things simple and costs down, says Van der Merwe. “The biggest thing for us is making sure our capital is low. You need to be a low-cost producer and if you can’t do that you’ll be priced out of the market. In a sense, there is nothing exceptional about our project: it’s really very simple,” he concludes.
Written by Becky Done, research by Jon Bradley
DOWNLOAD
Kudumane-EMEA-Dec12-Bro-s.pdf