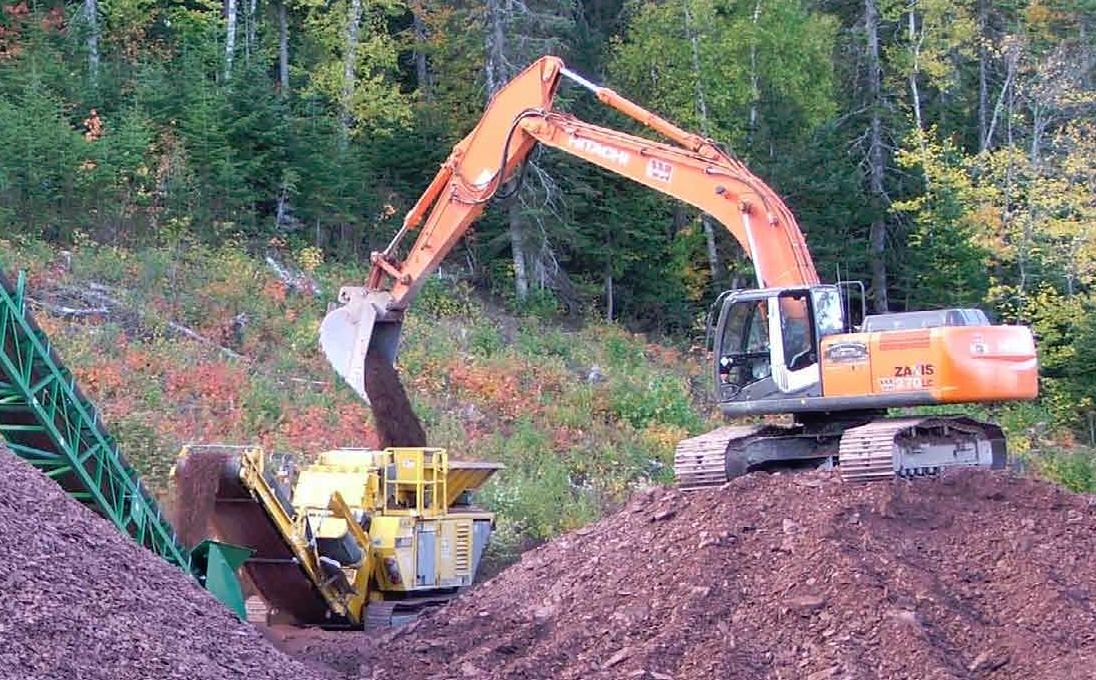
From its headquarters in Quebec, Canada, one company is revolutionising the way in which alumina and other high value materials are recovered from the earth. President, chief executive officer and director, Richard Boudreault explains.
Be it its breath-taking natural beauty, cultural diversity or its rich heritage that still resonates through a predominantly French-speaking population, there is much that the world already knows about Canada’s largest province, Quebec. What is perhaps less well known is the fact that Quebec holds the distinction of being the world’s third-largest producer of aluminum, behind China and Russia.
Running along the south shore of the Saint Lawrence River, Quebec’s Gaspé Peninsula is the home of the Grande-Vallée property, a large aluminous clay deposit boasting a conservative estimate of one billion tonnes of indicated mineral resources in the first 100 metres of depth in one sector alone, as defined under NI 43-101. It is here that one Canadian company can today be found using state-of-the-art technology to revolutionise the industry.
“Technology,” explains Richard Boudreault, president, chief executive officer and director, “is what sets Orbite Aluminae apart. Fundamentally, we are a clean-tech company that is striving to make the unobtainable available.” The technologies used by the company for producing smelter-grade alumina from aluminous clay are widely recognised as the best and most environmentally sustainable to replace a significant portion of the higher-cost alumina that smelters across Quebec import annually.
“When we extract clay from the ground,” Boudreault continues, “over 99.9 percent of the material in the deposit is turned into a sellable product or steam, whether it is alumina, pure silica, magnesium or rare earths.” Producing high-purity alumina is another of the company’s foremost concerns. This hugely in-demand material is used to manufacture LED lights and is found in all sorts of electronic devices including lithium ion batteries.
Another element that is becoming of increasing importance is scandium. Generally used as a catalyst, scandium has a high potential for use within the aluminum and the electrical fuel cell industries. Perhaps more importantly, it is a material that, when combined with aluminum, becomes a part of a hexagonal crystalline structure that possesses similar structural, electrical and thermal qualities as titanium, but at a fraction of the cost and weight.
“Aluminum-scandium is definitely going to become the next big thing in the aluminum industry,” Boudreault says, “because it is very likely to impact the aluminum-lithium used around the world within the next five years.” Until now, the fact that scandium has only been produced in a small region of Scandinavia and Russia in soviet-era mines made this future scenario look impossible. Now that Orbite Aluminae has access to this once unobtainable material it expects to produce enough scandium to meet pent-up global demand.
Across the planet, alumina is becoming more difficult to extract as the sources of high quality bauxite are being depleted. Good sources of bauxite are characterised by having a minimum amount of silica present. When dissolved in a caustic solution, silica combines with aluminum and iron, binding solidly to become red mud, a highly toxic waste product of the 125 year old Bayer process. Typically, for every tonne of alumina recovered, two tonnes of red mud is produced during the Bayer process. Increasingly frequent accidents involving red mud have blighted many countries, destroying lives and the environment in the process.
Orbite Aluminae has therefore developed its own red mud remediation process using hydrochloric acid. After reacting with the acid, rather than bind with the aluminum and iron, the silica which is not soluble in hydrochloric acid, falls to the bottom of the mixture and is filtered out, avoiding the creation of red mud. In this unique technology, the acid is recycled at over 99.75 percent and reused in the process.
“Not only does our process enable virtually all of the aluminum present to be converted into alumina,” Boudreault enthuses, “it also allows for the recovery of other materials such as scandium, gallium and rare earths during the recycling loop. This recovery process has been so successful that we will soon be in a position to produce the equivalent of the world’s total annual production of gallium from just one of our facilities in that same time period.”
Orbite Aluminae’s red mud remediation programme follows the same principle that exists throughout the company and that is making the most out of the material in the ground. What it plans to do now is introduce this concept to the wider world by exporting and licensing its technology outside of Canada.
The question this does beg however is, why would Orbite Aluminae want its competitors to gain access to its technologies? The answer is surprisingly simple. “In the very near future,” Boudreault says, “we expect to see the costs associated with transporting alumina to outweigh the price of alumina itself. When that happens, producing alumina locally will be a much more sensible option.”
With the demand for high purity alumina soaring, Orbite Aluminae is already being challenged to increase its anticipated production levels. In order to meet this demand, the company is currently in the process of constructing its first, of what it expects to be several, high purity alumina plants, which is expected to be commissioned by the year’s end.
“The HPA plant will bolster our financial resources needed to take the business to the next level, which is the building of our first $500 million smelter-grade alumina (SGA) plant,” Boudreault states. “With ten of these SGA plants we would be able to provide 50 percent of the alumina imported into Quebec. Furthermore, we will make available high quality separated rare earths, rare metals and other strategic materials from a reliable and sustainable source. We expect the first of these plants to be operational in late 2014.”
“Apart from producing alumina and high-value by-products, the market is only now starting to recognise the waves being made by our red mud remediation programme,” Boudreault concludes. “On another front, we have also shown that we can treat fly ash generated at coal-fired power plants in our process to recover the alumina and other high value elements it contains. This is another way in which we are essentially turning garbage into plough share and is just one of many exciting developments we plan to bring to the global market in the near future.”
Written by Will Daynes, research by Daniel Finn
DOWNLOAD
Orbite-AM-Nov12-bro-s.pdf