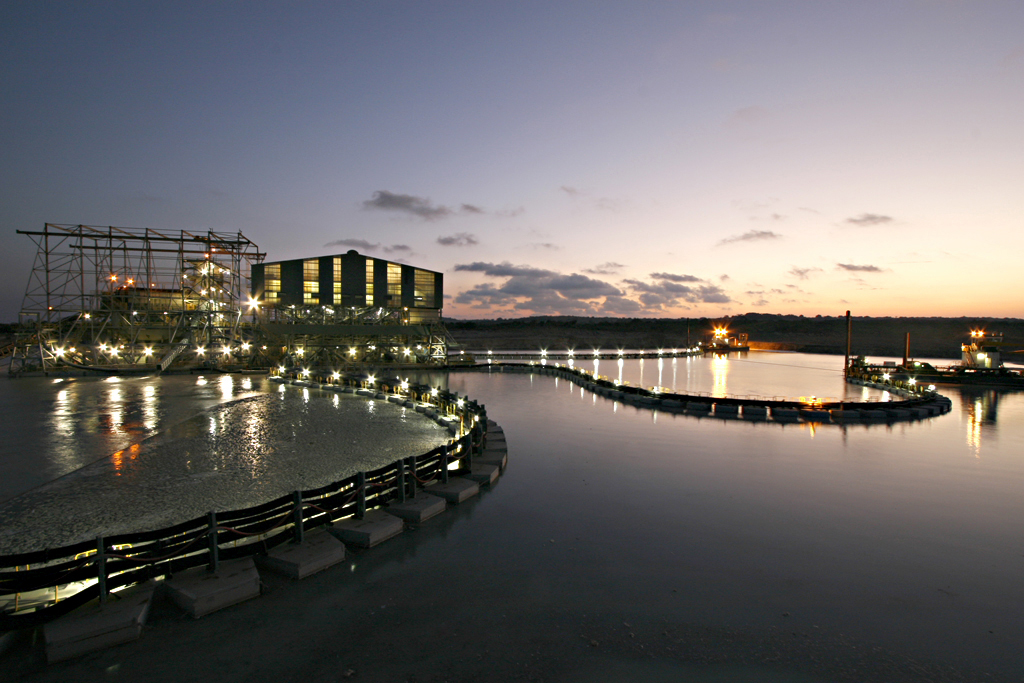
The world wouldn’t be quite as white as it is without an expanding titanium minerals mining operation in the wilds of Mozambique, as Alan Swaby learns from managing director Michael Carvill.
These days, when artists want a white on their palette, they usually choose titanium white. It’s the brightest and most opaque white there is and is sometimes called the ‘perfect white’. But despite titanium having been discovered in the 18th century, its use as a pigment came far too late for the old masters or anyone, for that matter, painting before about 1920.
Today, though, six million tonnes of titanium dioxide are used as paint pigments, and in a host of other applications from tile glazes to toothpaste, and demand is growing. So much so that one of the major suppliers of ilmenite and rutile—the two heavy minerals where titanium is to be found—is in the process of ramping up production by 50 per cent.
“At the current rate of production,” says Michael Carvill, managing director of Kenmare Resources, “we are sitting on deposits that could maintain mining here for 200 years. We are in the process of doubling our capacity which will take us from a seven per cent market share to around 10 per cent.”
The mine is literally in the middle of nowhere, 1,500 kilometres north of the Mozambique capital Maputo, in the province of Nampula, directly south of the Tanzanian border. In the 1990s, a freelance Czechoslovakian geologist identified the general area as promising and at his instigation, the Yugoslav government donated further geological investigation to Mozambique as a form of aid.
During the same sort of time scale, Kenmare was developing a portfolio of mining interests in various parts of the world. Kenmare as a company dates back to 1972 when it raised capital to drill for oil near the Irish town of Kenmare in county Kerry. Nothing ever came of this and the company went dormant in 1986 until bought by Carvill and his partners—largely because it was already listed on the Irish stock exchange.
Kenmare was invited to get involved with developing the Mozambique resources but rather than jumping in with both feet, offered to test the Yugoslav findings. “We drilled 22 holes,” says Carvill, “right next to holes that had already been sampled. Our analysis, though, differed widely from the previous picture. The lease was cancelled and we bowed out.”
Eventually, the Mozambique authorities went back and asked Kenmare to continue the exploration work, which resulted in huge deposits of minerals being found along the coast that were further defined during the 1990s. A feasibility study was completed in February 2001 which confirmed its commercial viability, yet it took another three years of work before a contract was placed in 2004 to build the Moma Titanium Minerals Mine.
“To indicate just how isolated this place is,” says Carvill, “everything on the project had to be taken to the site by ship because there are simply no suitable roads or bridges to afford an inland approach. It was like some grand D-Day landing. Just like D-Day, the planners underestimated the difficulty and the contractor lost money on what had been negotiated as a fixed price deal.”
The whole construction exercise proved unsatisfactory all round. The plant didn’t function as it should and as well as the contractor being out of pocket, Kenmare also faced additional expenditure getting the plant fit for purpose. Now, though, it’s running smoothly and processing 22 million tonnes of sand a year from which Kenmare has the capacity to produce about one million tonnes of saleable minerals.
The mining process is based on the use of two dredgers, working in an artificial freshwater pond approximately 800 metres long, 300 metres wide and up to 15 metres deep. The dredgers make cuts at the base of the ore face with high pressure water jets, causing the loose ground to collapse into the ponds. The mineral-bearing slurry is pumped by the dredgers to a wet concentrate plant floating alongside. By running the slurry down a series of spirals, clean sand is separated out, leaving the heavier particles free for further processing. The heavy metal concentrate produced at the mine represents about five per cent by weight of the total sand mined.
“We opted for this form of mining,” says Carvill, “because it gives much lower cost of production compared to dry mining methods. The whole site is compact and slurry is pumped over relatively short distances. Rather than having to rely on expensive diesel fuel, we get relatively inexpensive electricity from the Cahora Bassa hydroelectricity plant.”
From the pond, the slurry is then pumped overland up to the mineral separation plant and stockpiled for three or four weeks until it dries out naturally to around five per cent moisture content. In the processing plant itself, the final moisture is driven off by heating the sands to 120°C. After screening to remove oversize particles and remaining trash, the ore has to be separated into ilmenite and rutile—the first being magnetic and in the majority, and the latter non-magnetic.
“The refining process, proper,” says Carvill, “consists of repeated passes through electrostatic separators, each time removing more and more of the waste. The technology is simple enough but it requires constant attention and a sensitive hand on the controls to keep the plant working at high efficiency.”
There is a third mineral mined at Moma, although unrelated to titanium. Zircon is an important raw material in the manufacture of ceramics that saw a doubling of prices during 2011. This may well slip back as demand in China eases but last year Kenmare did very well from the 44,000 tonnes it exported.
On the environmental front, Kenmare’s policy is to meet not only Mozambican environmental requirements, but all relevant international standards, including World Bank standards. Clean tailings are straightforward to deal with as the coarse sand settles immediately. There is also a fine clay fraction (slimes) that settles less quickly. Slimes are deposited at the rear of the dredge pond where they are spread out for future rehabilitation.
As the dredgers mine the ore and the sand is deposited behind the mine pond, the pond gradually moves along and the land is rehabilitated. The course sand is contoured to match the surrounding geography and then covered with a layer of clay-rich slimes mixed with sand which helps the subsoil retain the necessary moisture and nutrients to aid re-vegetation. A final layer of stored topsoil—containing seeds, organic material and microorganisms—becomes home for a variety of plants and food crops.
2011 has been a good year for Kenmare. At the start of the period, ilmenite was achieving about US$100 per tonne but by the end of the year, prices for 2012 deliveries were hitting $300 to $400 per tonne. It seems the industry is moving away from multi-year pricing to a model of setting prices on a shorter term basis as demand outstrips supply. This is good for Kenmare, as is the rise in rutile prices—the other source of titanium oxide found at Moma. In the same period, prices have increased from around $700 to over $2,000 per tonne.
“Despite the downturn in Chinese real estate,” says Carvill, “we consider that the market for titanium feedstocks will remain strong—at least in the medium-term. Barring a precipitous drop in demand caused by another global financial crisis, it is hard to see how supply tightness can be relieved for some time to come. Production here can be ramped up any time we choose in order to track increasing demand.”
This is all good news for Kenmare which is sitting on one of the better bodies of ore anywhere in the world. It’s of a good mineral grade that doesn’t need to be upgraded before use and the mining operation is blessed with cheap power, abundant fresh water and no costly overburden to remove. With its own loading jetty in the backyard, Kenmare can ship product to customers at minimum cost.
This means that the go button for phase II of the site’s development—a 50 per cent increase in capacity—has now been pressed and is well underway. “The expansion will be a half scale mirror image of the dredge-based mining operations that already exist,” says Carvill, “which will give us the possibility of another ramp-up in production as soon as we identify that supply is being outstripped by demand.”
As well as increasing throughput by putting in another bank of ilmenite separators, the processing plant is trying to remove some cost elements by installing a wet high intensity magnetic separation circuit at the front end. This equipment is in common use within the mineral sands industry and will replace the dry primary separation stage and its associated costs by separating magnetic and non-magnetic fractions within the heavy mineral concentrate while in a wet state.
Expansion will increase design capacity by approximately 50 per cent all round, resulting in an increase in production of ilmenite from 800,000 tonnes per annum (tpa) to 1.2 million tpa; zircon from 50,000 tpa to75,000 tpa; and rutile from 14,000 tpa to 22,000 tpa. The $300 million expansion project is well underway and already the beaches once again resemble D-Day as heavy pieces of equipment are landed by sea—the roads still remaining not much better than they were.
In other respects, too, the area is benefitting from Kenmare’s presence. Since 2004 it has sponsored the Kenmare Moma Development Association (KMAD)—an independent not-for-profit development organisation which supports and contributes to the development of the communities close to the mine.
While Kenmare contributes most of the cash needed, it does so with help from other aid bodies and voluntary involvement of Kenmare’s employees both in Mozambique and Ireland. KMAD focuses on three categories of projects. First, it facilitates economic opportunities by encouraging local farmers to provide the food the mine needs. Then, it sponsors ongoing education programmes designed to slow the spread of HIV/AIDS, a serious problem in Mozambique as in so many African countries. The final strand in KMAD’s contribution is to do what it can in improving rural infrastructure. Based on community needs, it contributes to health facilities or school resources. Anxious not to create any white elephants, KMAD will only become involved with a project when it is clear it has a sustainable future.
The world over, rural areas tend to be at the bottom of the food chain, but with the size of Kenmare’s resources in Mozambique there could be a little part of Ireland there for many years to come, making a contribution to the country as a whole and the local community in particular.
DOWNLOAD
Kenmare-EMEA-Apr12-Bro-s.pdf