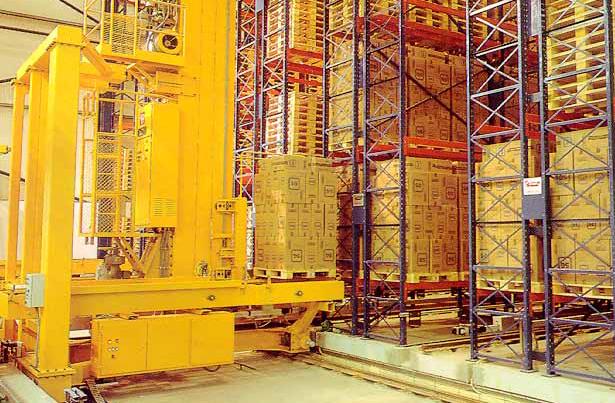
Godfrey Phillips India is one of the largest players in the Indian cigarette industry, with an annual turnover of over Rs 3000 crore, or $620 million. Incorporated in 1936, the company has two major shareholders: the KK Modi Group, which holds the largest share, and the American tobacco giant Philip Morris.
Godfrey Phillips India has its headquarters and a major manufacturing plant in Delhi; however, Mumbai is an important hub for manufacturing, distribution and research, with a long-established factory in the Andheri district and a state-of-the-art R&D centre. The company’s core business is manufacturing and marketing cigarettes for the Indian market, and it has in its portfolio some of the most popular cigarette brands in the country. Godfrey Phillips India has an arrangement with Philip Morris to manufacture and distribute its brands, including the iconic Marlboro cigarettes, available from around 65,000 retail outlets across India.
For many years, Godfrey Phillips Indiahas been exporting cigarettes as well as cut tobacco. Many countries from the Middle East to West Africa, South East Africa, South East Asia, Eastern Europe, Australia, South America and Central America have been added to the portfolio and the company’s International division is continually making efforts to expand its overseas footprint.
International expansion is one of the strategic goals behind the launch later in 2011 of a brand new factory that has been built from the ground up at Rabale in the suburbs of Mumbai. “One of the problems with our other manufacturing facilities is that they are limited in their potential for expansion. Andheri has seen urban development to such an extent that the 60-year-old factory is now hemmed in on all sides with residential areas,” says Pradip Mittra, executive vice president of Operations. “The traffic in the area is heavy at the best of times and getting raw materials in and finished products out in large containers is frankly a nightmare!”
The company needed more production capacity to satisfy the demands of the domestic market, but equally importantly, to support the drive to sell product overseas. The Rabale factory has excellent road links to the new Mumbai port that has been constructed further out from the city to relieve congestion on the old Bombay harbour. “We have tried our best to incorporate the best and most modern technology in this factory,” says Mittra.
Just as the company recognised two strategic drivers in deciding to invest in the new site, (measuring 44,000 square metres with a 21,500 square metre factory building) it was designed with a two key objectives in mind: firstly to deliver the best quality products to the consumers and secondly, to improve productivity to a new level. “It incorporates three major new technologies,” Mittra explains. These correspond to the three main areas of production: the primary manufacturing which prepares the cured tobacco leaf for production, the secondary manufacturing which involves cigarette making and packing, and the warehouse and despatch area.
Equipment for the primary processing plant is arriving and being installed ready for commissioning by the end of 2011. The equipment supplied by COMAS of Italy will take the bales of tobacco supplied from Godfrey Phillips’s threshing plants in southern India, unpack the leaf, cut it, dry it and feed it through to the cigarette manufacturing plant. “The cut tobacco will be just about the highest quality you can get, and we are also going to upgrade the primary processing at our Delhi plant—we want to make sure the quality is consistent across the board,” he says.
Construction work is complete at the new plant, and all of the secondary equipment is now in place. Cigarette production will in fact commence by October, a couple of months ahead of the primary lines. “On the secondary side we have already invested in high tech, high speed cigarette making and packing machines in both the Delhi and Mumbai factories. In designing the Rabale plant we went a step further in that we have the machines linked up.” This results in less handling of the product and fewer changeovers, giving better quality. An additional benefit is reduced cost and higher productivity because fewer people are needed to man the automated lines.
The third leg of the technology tripod is the handling and storage system which has to deal with three classes of materials, Mittra explains. “Firstly, cut tobacco comes into the plant compressed into conventional C48 cardboard boxes; secondly there is all the non-tobacco material (NTM) that is used in cigarette making like papers, filters and shells; and thirdly the finished goods—cigarettes packed in master cases ready for dispatch. It’s a complex handling scenario, and to manage it we have invested in the first fully automated storage and retrieval system (ASRS) ever to be installed in a tobacco plant in India.” The stack is 20 metres high, with a six metre deep basement, he says, with computer controlled robotic cranes to place stock items and retrieve them when called for by production.
All material coming into the new plant, whether tobacco or NTM, now has to be supplied on international-standard pallets. “We had to work with the suppliers well ahead of installing the ASRS in order to make sure they could comply,” says Mittra. And to achieve complete traceability through the supply chain, from bale to cigarette packet, the same suppliers will have to have software in place that can talk to Godfrey Phillips’s Oracle ERP system. The system was implemented some two years ago with financials and inventory management and has been progressively rolled out to cover production and sales.
Rabale was the first factory to register with the Indian Green Building Council when it launched its Standard for Green Factory Building in 2009. Like the ISO 14000 accredited Ghaziabad and Mumbai units, it has already adopted the use of environmentally friendly measures such as recycling water, 95 per cent rainwater harvesting, recharging pits for ground water table levels, insulated roofs, screw compressor chiller, 6-12-6 glass with low U-value on windows for reducing HVAC heat load, and using solar power systems; but as a new construction it has also been built using sustainable materials selected for the lowest carbon impact, namely low density fly ash blocks and low VOC paints.
Concern for the environment goes hand in hand with good employee relations. “We have invested so much in technology, but our biggest asset remains our people,” asserts Mittra. People working for Godfrey Phillips India are valued, and their opinions count. “We have systems in place that we have learned from our Japanese friends, such as kaizen teian (continuous improvement based on workers’ suggestions), 5S, TQM and six sigma. It has given a sense of empowerment to the employees—the feeling is that they are contributing not only with their hands and their skills, but with their thinking too.”
A year-round training programme promotes morale as well as productivity. Another technique taken from the Japanese is to train experienced employees to school the newer recruits. It does wonders for employee engagement, Mittra says—and with a reputation as one of India’s best employers, Godfrey Phillips India should have no difficulty filling the 100 or so skilled jobs the factory has created. www.godfreyphillips.com
DOWNLOAD
Godfrey-EMEA-Aug11-bro-s.pdf