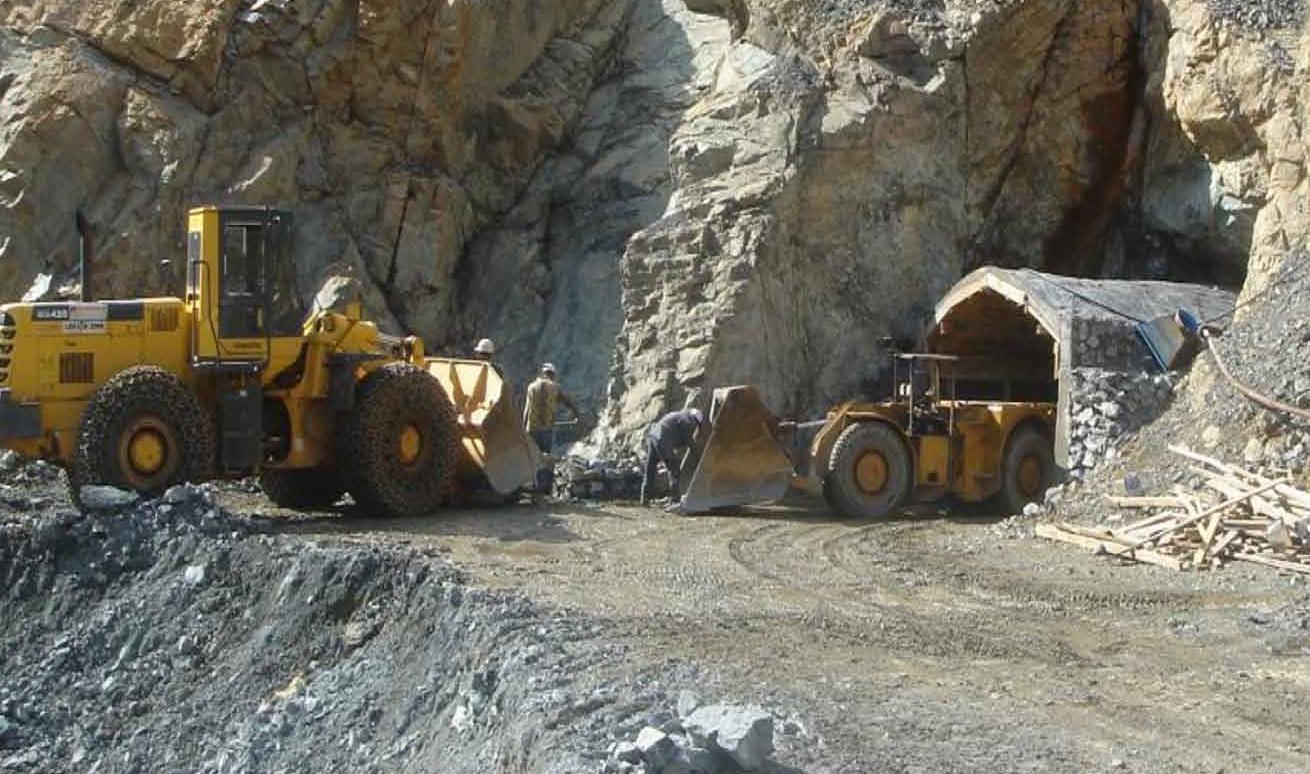
One of Turkey’s most important home-grown mining companies is weathering the decline in demand for chromium ore and continuing to supply its customers year-round.
There’s an interesting tale relating to the discovery of chromium ore in Turkey. Apparently, in the 1930s, a German company was mining and smelting copper in the Elazig region of the country and local inhabitants were making some extra cash by collecting wood in the hills that the Germans then converted into charcoal. So the story goes, one such forager needed a rock to counterbalance the panniers straddling his donkey for the trek down the mountain. He didn’t need the rock to go back up, so left it lying around, only for it to be noticed by a sharp-eyed German engineer who recognised what he was looking at. In true Cinderella fashion, the local worker was found, the source of the ore identified and the Germans switched their attention from copper to chrome—at that time, a particularly strategic ore with many geopolitical implications.
“It probably meant,” says Dr. Alp Malazgirt, recently appointed chief executive officer of Yildirim Holding, “that the Germans had not focused on chromium mining until it became a strategically important metal. I’m not a trained geologist but on an inspection tour of new leases we have acquired near Adana’s Aladag region, it is possible to see many such lumps of chrome ore and I am sure it was even in greater abundance at Elazig back then.”
After the Second World War, the Turkish state continued to run Eti Krom, as the mine and processing plant was known, but never very profitably. At the start of 2000, the country began a wholesale privatisation programme and in 2004, when the mine was losing over $100 million a year, the brothers Yildirim took over the mine. “Today,” says Malazgirt, “Eti Krom is the flagship of all Yildirim operations. It’s the largest and richest chromite source in the country and generates much of the over $1 billion in revenue for the group.”
The mine itself is located on a 200-hectare site 55 kilometres from Elazig. The main activities there can be summarised as open pit and underground mining of chromium ore, a chrome beneficiation along with a briquetting facility, production of high carbon ferrochrome, and the recovery of ferrochrome from slag. In total, the Eti Krom operation numbers around 80 chrome ore mines with 20 of them currently active. Proven reserves top 100 million tonnes, with current annual production capacity of about 1 million tons of chromium ore. Ferrochrome production capacity is 150,000 tonnes and the smelting operation takes place in four furnaces, two open and two new semi-closed arc furnaces near Elazig, all of which have been updated and modernised in the past five years.
Turkey has no shortage of chromium mines but what sets Eti Krom apart is the high quality of the ore. There’s a very high ratio of 2.7:1 chrome to iron but even more desirable is the low silicon content. “Silicon can be removed readily,” explains Malazgirt, “but at a higher cost as neutralising the silicon needs more carbon and therefore more coal. The phosphorous content of our ore is also low which means it is ideally suited for the very high grades of stainless steel.”
These characteristics have helped Eti Krom weather the decline in demand and the suppression of prices seen since 2008. At the time, chromium ore was fetching around $750 per tonne; now the price is either side of $270. Nevertheless, through a combination of operational hedging and optimising its mining and manufacturing units, Eti Krom has remained viable. Productivity and process improvements have led to increased flexibility and a low cost operation. Eti Krom has used its financial strength and steady cash flow to make capacity-increasing investments with zero leverage.
Eti Krom remains an important partner to its customers as it is the only Turkish chrome ore supplier that can produce chrome ore all around the year, without any suspension, even through the tough winter season. By stockpiling product in 18 strategically located warehouses, it can rapidly supply customers worldwide with the ferrochrome they need.
When it comes to ferrochrome, the market for standard grades is now dominated by the Chinese, who have taken over from South Africa as the world’s greatest producers just recently. “South Africa has 70 per cent of all known chrome ore,” says Malazgirt, “but that hasn’t stopped China investing hugely in its own ferrochrome production. Of course the power shortages in South Africa haven’t helped, as the smelting process is extremely energy-hungry.”
Electricity supply is just as critical for Eti Krom but more under control. The grid supply is reliable but is gradually being supplemented with Eti Krom’s own generated electricity. “Yildirim has been importing coal since 1995,” says Malazgirt, “and we have a very experienced team which knows how to get the best out of its partners. Next year we shall build a new electricity generation plant near at Elazig using coal imported from South Africa, Colombia, or Russia—the best source of coal for the high temperatures needed in the smelting process. What we don’t need for our own purposes will be fed back into the grid.”
In a relatively short period of time, the Yildirim brothers have created a group with a very wide range of interests (10 sectors in all), many of which provide synergy for the mining and fertilizer operations. Yildirim has its own fleet of 18 ships, of which 9 are tankers and the rest are dry bulk carriers, so has the means of shipping product to customers or importing those commodities it needs. In the case of coal, ore is shipped in wagons down to the Mediterranean ports for export and then coming back, the wagons will haul imported coal for the future 200 MW power generation plant. Hence, the synergy will be accomplished by combining all, or most of the steps in the ferrochrome operational supply chain.
Despite these interlocking divisions, Yildirim has yet to take any interest in manufacturing, although it comes as a great pleasure to Malazgirt to note the extent to which Turkey is developing its ability to be self-sufficient. “When the crushing and beneficiation plant was originally built at Elazig,” he says, “all the technology had to be imported. Now we are seeing that much of what a plant like ours needs can be produced within the country.”
Such improvement in manufacturing capabilities will be good news for the government also. Considering the number of new mining developments that have been seen over the past decades, the mining sector still only accounts for one per cent of the country’s GDP. By 2023, the target is for mining to generate five per cent of the country’s wealth. In other words, there will be plenty of work for local suppliers. But for this target to be met, Malazgirt is warning that the country’s bureaucracy needs to become as efficient as its manufacturing.
“Getting approval for anything is a slow process,” says Malazgirt. “We have licenses for 20 other sites all over Turkey that are waiting for development and which could be creating new jobs and export revenue. Most of the concern is for environmental protection of the countryside, which is admirable, but the process needs to be streamlined.”
Eti Krom already has good credentials in trying to create a sustainable operation. We’ve already seen that by tapping into Yildirim’s logistics network, coal is being imported and finished products exported with the maximum degree of efficiency—thereby minimising its carbon footprint.
As electricity is the largest single cost associated with smelting, becoming self-sufficient is high on Eti Krom’s to-do list. In addition to the coal power generation plant underway, the operation is also trying to recycle some of the energy found in the hot gases produced during smelting. A system is currently being built which will collect 600°C waste gases from the smelter, filter them and cool them down to 400°C and then use them to power the boilers. This way it is hoped that 5.5MW of electricity will be produced in a clean, closed circuit.
A by-product of any smelting operation is the impurity carrying slag that forms on the top of the molten metal. In the case at Eti Krom, the chrome content is already very low—at no more than four per cent. Nevertheless, slag is being recycled in order to re-claim as much of the chromium as possible. When the last drop of value has been wrung from the slag, it can still be processed for secondary purposes. Rather than disposing of it as waste, Eti Krom is investigating ways in which the slag can be put to good use, for example, as a wear-resistant additive to concrete.
Although there is no shortage of job opportunities in the mining industry in Elazig province, Eti Krom remains the most important employer, with currently around 1,000 people on the payroll. It’s the largest source of tax for the city and the whole of the province and its long history makes it an important part of the countryside’s social fabric.
“Eti Krom has been part of Elazig life for as long as most people can remember,” says Malazgirt, “something that Yildirim is keen to maintain. As well as supporting local institutions such as schools, the group has a major project underway to convert one of the most important historical buildings in the city into a museum, celebrating the region’s mining heritage.”
What a pity the lump of chrome ore that started it all off can’t be available as the principal exhibit.
Written by Alan Swaby, research by Abi Abagun
DOWNLOAD
ETIKrom-EMEA-Oct12-Bro-s_0.pdf