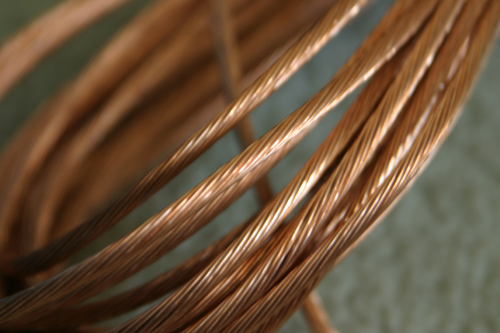
Before he established Er-Bakir, A. Nuri Erikoglu had already forged his own reputation through the building of hand-crafted home purpose copper products including boilers, braisers and trays. A visionary in many ways, Erikoglu was one of very few individuals to foresee the future potential of copper. With this vision and his unique entrepreneurial spirit he would go on to create Er-Bakir with the mission of producing copper wire in electric cable, a product now used on a mass global scale in all areas of life.
With Er-Bakir existing as a small workshop for only a couple of years it was in 1984 that the company set out along the road to transformation when Erikoglu entered into a partnership with close friend and respected industrialist, Cafer Sadik Abalioglu.
In the almost three decades since the partnership was formed Er-Bakir has undergone a period of significant expansion and development. In 1985 the company possessed the capacity to produce some 32 tonnes of wire rod per month, whereas today it boasts annual production of approximately 200,000 tonnes. In 1985 Er-Bakir also commenced with the export of its products with its first deliveries being made to Iraq and Iran. Fast-forward to 2013 and the company is now exporting to 30 technologically advanced countries.
Years of continuous investment have brought Er-Bakir to the point where today it has one of the largest electrolyte copper wire production facilities in the world. From this facility the company produces all manner of copper wire based products, from wire rod to braid wire. Er-Bakir’s copper wire rods are produced in its continuous casting unit and conform to ASTM B 49 and DIN 17652 standards. The majority of the wire rod it produces is used as inlet wire in wire drawing units, with the remaining product packaged in accordance to its customer’s individual requirements.
Er-Bakir’s single copper plain wires are processed, annealed or hard, in specially designed rod breakdown machine groups. They can then be used as inlet wire in other units of the wire drawing plant, sold packaged in steel reels or packed in cartons or steel baskets. These wires can also be used as inlet wire for tin or nickel plating.
Other single wires produced by the company are tin and nickel plated copper wires. Wires tin plated by electrolytic plating machines are packaged either in carbon baskets or reels before being directly sold to customers, or placed in steel baskets for use in the wire drawing unit of Er-Bakir’s plant. These wires are produced with dimensions ranging from one millimetre to 2.60 millimetres and can be tin plated to a wall thickness of 25 microns.
Similarly, wires that are nickel plated are packaged for direct sale or put to use in the company’s wire drawing unit. These wires come in dimensions ranging from 0.80 millimetres to 2.60 millimetres and can be nickel plated up to 27 percent by weight. Both intermediate and fine tin and nickel plated wires are also able to be packaged into reels of various sizes and dimensions that meet specific customer demands.
Elsewhere inside its facility bare, tin and nickel plated wires drawn by the company’s drawing machine group are wound onto steel or plastic reels, before being reduced in diameter to between 0.05 millimetres and 1.00 millimetres by being put through a cold working process and then annealed. As many as 24 wires can be processed at the same time and then wound onto reels by static or dynamic methods. These products are sold directly in this form or can be used as inlet wire for bunching or bobbin machines.
Bare and tin plated wires manufactured by bobbin wire take-up machines on the other hand are coiled onto four bobbins simultaneously. Bobbins are then packaged in 12 carrier and 16 carrier boxes.
Bare, tin or nickel plated annealed wires processed by single and multi-wire drawing machines are used as inlet wire for bunching machines. These wires are bunched in double twist, single twist, Planet Strander and Rigid Strander machines in cross sections, with areas ranging from 0.05 square millimetres to 360 square millimetres. They also come in various geometrical shapes and in pitches in accordance with the customers’ requests and standards, then wound onto steel or plastic reels before being transported away from the facility.
Er-Bakir’s products are sold across Europe and throughout the Americas. Their products also play a vital role in the operations of a number of Eurasian companies based in countries including Kazakhstan and Israel.
As a way of both supporting its international clients and extending its own reach the company has sales agents based in all of its core export markets that ensure that it engages its clients on a one-to-one basis and has the ability to identify new opportunities as they arise. The company supplies to a host of major industries including the automotive and electronics sectors, with its products currently being sold to several illustrious organisations including the likes of NASA and Boeing.
Away from its facilities, Er-Bakir has been involved, and continues to be involved, in several notable social responsibility programmes. One of its greatest accomplishments was the construction of the Er-Bak─▒r Science High School in 1999. Funded by $1.2 million of investment capital the school is today managed by the Ministry for Education and provides education to around 500 students.
More recently, in November 2009, the company brought its waste water treatment plan into operation. The plant itself has a water processing capacity of 40 cubic metres a day, with the treated water free of metal ions and thus presenting no threat to the environment whatsoever.
The plant itself also houses a separate unit for destructing waste emulsions. Waste emulsions are processed in this unit so that oil is separated from the water. This means that harmful waste is not subsequently released into the environment.
Operations throughout Er-Bakir are all very integrated in nature, allowing the company to make considerable cost savings and also control the quality of its activities. Having helped breed such positive results for its business over the years, there is little chance that the company will feel the need to change its ways anytime soon - and rightfully so.
Written by Will Daynes, research by Abi Abagun
DOWNLOAD
ErBakir-Euro-Manu-June13-Bro-s.pdf