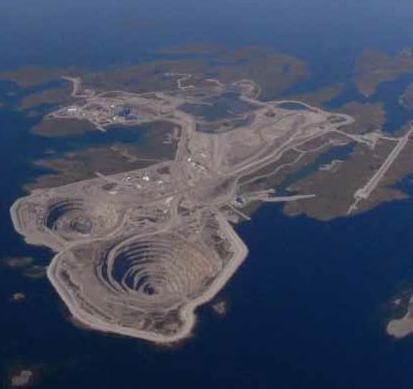
Created under intense heat and pressure, and delivered to the earth’s surface by volcanic action, diamonds are being mined in the icy reaches of northern Canada. Gay Sutton looks at the development of the Diavik Diamond Mine, the role of the luxury jewelry brand Harry Winston, and the positive legacy it intends to leave for the Aboriginal people.
The diamond has been prized for considerably longer than 3,000 years, not only for its exquisite beauty as a gemstone but also for its strength as a cutting tool. Its name is derived from the ancient Greek word adamas which means unalterable or unbreakable – also the root of the word adamant. Until relatively recently, the majority of the world’s supply of these highly prized stones came from alluvial deposits in India; in other words they were simply picked up from the shores of the Penner, Krishna and Godavari rivers. Later alluvial deposits were found in Brazil but it wasn’t until the focus shifted to Africa in the 1880s that true diamond exploration began. Today, Canada has become a major producer of high quality diamonds, too, and the Diavik Mine is one of its most productive mines.
Diavik lies almost 200 miles north east of Yellowknife, the capital of Canada’s Northwest Territories, on an island in beautiful Lac de Gras. The area first hit the headlines in 1991 when diamond-bearing kimberlites were discovered at Point Lake near Lac de Gras, initiating the famed Canadian Diamond Rush. “Finding these diamond ore bodies is extremely difficult,” explained Bob Gannicott, chairman and CEO of the international jeweler Harry Winston Diamond Corporation, part of the joint venture that owns the Diavik Diamond Mine. “Since 1867 when the first hard rock diamond deposit was discovered in Africa, only 50 viable kimberlite sites have been discovered and put into production,” he said. “In comparison, some 1025 gold deposits have been exploited.”
The majority of natural diamonds are formed as crystals some 90 to 120 miles beneath the earth’s surface, in the intensely high pressures and temperatures found in the earth’s mantle. It takes an astonishing 1 billion to 3.3 billion years for the crystals to form. But they only become accessible to us when thrust up close to the earth’s surface through volcanic activity, when the magma is allowed to cool into diamond bearing kimberlite or lamproite. In Canada’s case, this volcanic action occurred some 55 million years ago.
The rarity of diamonds is due to the magma from these specific diamond forming regions of the mantle seldom reaching close enough to the earth’s surface, and when it does, very little of it contains diamonds in viable quantities for mining.
Gannicott’s company, then known as Aber Diamond Corporation, staked a claim to the Diavik block in 1991 and began a programme of exploration in partnership with Kennecott Canada – the exploration arm of international mining giant Rio Tinto plc.
By 1995, the partners had identified four diamond bearing kimberlite pipes located in what can only be described as a most challenging position – on the bed of a large, pristine lake. Undaunted by the engineering innovations that would be required to construct a mine surrounded by water and ice in temperatures that can drop to -50oC in the depths of the winter, the partnership moved on to the mine development stage.
A formal joint venture was formed between Yellowknife-based Aber (40%) and Rio Tinto (60%). Under the terms of the agreement, Rio Tinto would manage and operate the mine through a wholly owned subsidiary Diavik Diamond Mines Inc which would be headquartered in Yellowknife. Once production began, the diamonds would be shared 40/60 between Aber and Rio Tinto.
Environmental and feasibility assessments along with permitting and licensing were completed over a period of some four years. The area was no stranger to mining, however, and previous experience had been negative. Gold mines in the region had left a legacy of pollution, and the local Aboriginal populations had failed to benefit from the mineral resources discovered on their traditional hunting grounds. “So we set the bar extremely high at the permitting stage,” explained Marc Cameron, Diavik’s VP Operations.
An environmental baseline study, completed in 1997, and a rigorous environmental assessment process have been a sound basis for ongoing environmental monitoring. A comprehensive Environmental Agreement has been signed with the five Aboriginal organizations and governments in the area which exceeded the requirements of the legislation at that time. In parallel with this the company has signed additional agreements to ensure they benefit from the mine’s presence on their land. “This isn’t our land. We have access rights to it at best, for the life of our operation. We would like our behavior here to become a valuable legacy for the Aboriginal people,” Cameron said. The agreements became a part of the license to operate and permission to construct the mine was granted in September 2000.
Some $1.3 billion was spent on mine construction during those first three years, and this included processing and recovery plants, administrative and accommodation buildings, a full range of utilities such as power generation, boiler, water supply and wastewater treatment plants, massive fuel storage tanks and an airstrip capable of handling Boeing 737s and Hercules transport aircraft.
The challenges of a construction project on this scale and in this location, however, cannot be overstated. The climate, for one, is extremely harsh. Officially classified as a desert, the region receives less than 10 inches of rain a year, and most of that falls as snow. There is rarely a cloud in the sky, which can be a boon in the summer when the sun goes down for only a few hours of twilight a day and temperatures rise to a balmy level. However the winter nights are long andtemperatures can plunge as low as minus 50oC.
The first major challenge facing any operation in this environment is a logistical one, and this applies to all phases of operation from original exploration to mine closure. Surrounded by a landscape of lakes and rocks, the mine is only accessible by air for most of the year, which is not a financially viable means of transporting fuel, equipment and materials to the site. To address this issue, Diavik, BHP Billiton Diamonds Inc. and De Beers Canada Inc. (who operate the nearby EKATI and Snap Lake diamond mines), operate together in a joint venture to achieve an incredible feat of engineering, creating a cost effective method for transportation.
Each January, a massive 360 mile long winter ice road, 87 percent of which runs directly across frozen lakes and ponds, is constructed between Tibbitt Lake at the end of the highway from Yellowknife, and Contwoyto Lake. Although only open for two months in every 12, the road links each of the mines with Yellowknife and Western Canada and is very busy, successfully hauling up to 11,000 loads in a very short period of time. Built to withstand high levels of heavy traffic, it’s shared with a variety of other groups in the region, from exploration companies and tourism outfitters to the Aboriginal hunters harvesting meat for their families.
During the mine construction period, the entire year’s supply of construction materials and heavy plant had to be trucked along this temporary lifeline. Now the mine is in operation, its importance has not diminished. It provides the most cost effective method for restocking the mine’s yearly requirement of fuel, explosives, replacement equipment and spare parts – and more recently, cement for backfilling the underground mine.
Perhaps the greatest engineering achievement of the construction period, however, was designing a reliable, safe method for mining on the bed of Lac de Gras ensuring that there would be no ingress of lake water into the mine and no impact to the delicate environment of the lake.
The solution the panel of engineers devised was highly innovative and consisted of a massive 2.4 mile long water retention dike to surround the first open pit mining site, the A154, and its two kimberlite pipes. It earned Diavik the Professional Engineering Award of Merit from NAPEGG, and the Canadian Council of Professional Engineers’ National Award for Engineering Achievement. Built by teams from Italy, Germany, Canada and the US, the design solved a whole range of problems such as how to maintain the permafrost beneath the walls during the summer, where the dike crosses islands. “Many of the construction methods had been used in isolation in other areas across the globe, but they had never before been combined into one,” said Cameron. “We then had to complete a significant portion of the construction project during a four month period – during the open water season.”
The mine went into production in January 2003. Capable of processing over 2 million tonnes of kimberlite ore annually (only one part per million of which is a diamond), the mine reached its first milestone by the end of May, by which time it had produced one million carats of diamonds, the vast majority of which are high quality jewelry grade stones. A second dike, the A418, was then constructed around the third ore body and that went into production in 2007.
Once the kimberlite has been mined, the ore is processed on site to extract the stones which are then sent to Yellowknife. Under the Joint Venture agreement, 40 percent are dispatched to the Harry Winston sorting facility in Toronto, and 60 percent are sent to Rio Tinto’s sorting facility in the world’s diamond capital, Antwerp. From this point, the two companies’ business models diverge in an interesting way.
Rio Tinto is a mining conglomerate with global reach and a presence in a wide range of mining disciplines from iron ore, coal and aluminum through to diamonds and uranium. Its interest ends when the product is sold on. Currently, the larger part of the company’s market is in the United States, although the aim is to diversify and move towards a broader customer-base that includes a strong Indian and Chinese presence.
Aber, by contrast, began in exploration, and has established an unusual and forward thinking business model that included a complete rebranding exercise. “The rough diamond market is not like the gold market where you can see the price in the paper in the morning. Rough diamonds are more akin to individual mineral specimens, and are grouped together in categories and then sold,” said Gannicott. “We believed that by buying into a jewelry business we would gain valuable market knowledge in terms of asking prices and trends, and this would provide the best route to market for our diamonds.”
For Aber, the timing of its search for a partner was perfect. Harry Winston, one of the world’s most prestigious branded diamond jewelers, and supplier of high-end jewelry to the stars – the renowned Taylor-Burton diamond and the Hope Diamond are just two examples – was looking for a partner. Months after Diavik went into production Aber began negotiations to acquire a controlling 51 percent interest in Harry Winston, and the deal was completed in April 2004. By 2006 the company had acquired 100 percent ownership of the luxury brand and made the decision to rebrand Aber as Harry Winston, combining this with floating on the New York Stock Exchange in 2007. The business reasoning behind the move has proved to be impeccable.
“The retailer’s business informs the rough diamond sale so we get a premium price that’s always in step with the market. And viewed the other way round, having a supply of rough diamonds from a place with the political stability of Canada gives us a privileged entry into the diamond market and provides security of supply for the top end material that the Harry Winston jewelry and watch business requires,” Gannicott said. “It’s not a vertical integration model as we don’t engage in cutting and polishing the diamonds.” In fact, rough diamonds are not sold directly to the jewelry business, but to customers mainly based in India, and others in China and Israel.
While mines have a finite life, Diavik has been operating for eight years, and is now transitioning from an open pit mine to an underground mine to extend the mine life to 2021. The transition, which has a price tag of some $800 million, has so far included the construction of over 12 miles of tunnels, rescue bays, washrooms, ventilation systems, repair shops, vertical tunnels for ventilation and water removal, pump stations and storage areas. On the surface, there have been a series of expansions and new developments. A new crusher and backfill plant have been constructed, along with a new accommodation block. Waste water treatment and power generation capacity have been doubled.
The first pit to make the transition was the original A154. Last year, open pit mining was drawn to a close, and underground mining commenced. The plan is to close the second pit, A418, in 2012 and transition that to underground. As with all mining, though, the process is a long learning curve.
“In the south pipe, we are in the process of trialing a very different mining method to the one that was originally planned,” Cameron said. Called sublevel retreat, the method will enable the company to remove ore more cost effectively than originally planned, and the method has been made possible by the geology of the surrounding rocks. “We then plan to trial the same method in the A418 next year.”
Going underground, of course, has required a whole new way of operating, and a series of internal campaigns has been run to realign and retrain the workforce in the new mining practices and to manage the transfer from open pit to underground mining.
As with all forms of mining, the day to day operational activities incur various degrees of risk, and good safety practices are expected of any global mining company. At Diavik, safety is driven from the very top and has become so much an integral part of company culture and operational standard practice that it has won the company a whole range of national and international awards. “Safety is truly our greatest value, but I suppose you’d expect me to say that,” said Cameron. The reality, however, matches the values of the company. Safety is ingrained into staff from the moment they begin their initial training, and for many this can be quite an overwhelming experience. “For new employees coming from say the construction industry or a small mining company, that first month is one of significant change. We have multiple layers of safety programs, and they can be challenging for some to work through, but everything we do is to prevent a fatality or major disabling injury.”
Diavik’s safety management processes are derived from those of its parent company Rio Tinto, which have been developed and honed over many years and draw on the company’s long experience in all forms of mining. As with all Rio Tinto companies, those processes are then adapted to each mine’s operations and applied through a set of stringent standards. It begins with an extensive education for the workers and is embedded through measuring ongoing performance, reviewing systems and programs and setting continuous improvement targets.
The results at Diavik are impressive and have earned the company the national John T Ryan safety trophy in 2009. “In 2009 we achieved our best safety record in the life of the mine, and then in 2010 we beat that. Our lost time injury frequency rate across the entire operation was 0.08.” As a result, Diavik was nominated for the CEO Safety Award at Rio Tinto. “As a relatively small business unit within Rio Tinto, which has over 77,000 staff in more than 40 countries, this was a significant recognition for us, and a huge accomplishment and achievement by our workforce.” But the focus on safety continues, with the goal of bringing the injury rate to zero.
Safety and care for the environment are certainly deeply appreciated by the local Aboriginal people who have been major beneficiaries of the mine. “When the Diavik mine opened the timing was just right for us,” explained Roy Erasmus, CEO of Det’on Cho Corporation, the business arm of the Yellowknives Dene First Nation. “Two of the largest gold mines in Canada, the Giant Gold Mine and the Con mine which had operated here for over 50 years had just closed. The Giant Gold Mine had left one of the largest contaminated sites in Canada, and the Yellowknives Dene received no benefit from the mine at all.”
Mining companies operating in Canada are expected to take part in impact benefit agreements for developments on Aboriginal lands. From the very beginning, Diavik worked closely with the five local Aboriginal organizations and signed a series of Participation Agreements with each, the goal being to ensure that the local communities received benefit from the wealth generated at the mine. Perhaps even more significantly, the focus was on active engagement with the five organizations and their business arms, to ensure the ability to generate proficient skills and businesses that would continue to sustain communities well beyond the life of the mine.
“We began with a lot of community-based training programs,” explained Colleen English, Superintendent, Sustainable Development and Communities. By identifying skills that could be developed in local communities, the company led construction projects that delivered infrastructure for the communities, leveraged local partnerships and developed the skills that could then be employed at the mine site. “And this really helped to foster ideas that resulted in on-going, formal training programs for the communities, while assisting Diavik in meeting our employment targets.”
The relationships have matured since then and continue to evolve. Today, close to 60 percent of the workforce is drawn from northern peoples, and many of the contractors working on site are part or wholly owned Aboriginal businesses. Of these, a number are dynamically expanding beyond Diavik, and becoming truly sustainable, such as site services provider Tlicho Logistics Inc., a 100 percent Aboriginal-owned company which has now expanded into the construction industry as well as other operating mines in the region.
At Diavik, these types of participation agreements have been supplemented by a socio-economic agreement to monitor and address any social or economic issues that arise, as well as an environmental agreement to minimize harm to the environment and incorporate traditional knowledge into the scientific understanding of the environmental impact of the mine’s presence. These two agreements also provide for their own boards to oversee agreement implementation and they are composed of representatives from the five Aboriginal organizations, governments and Diavik. This allows for a unique opportunity for community members to provide recommendations on operational and management decisions.
The current phase of underground expansion has extended the life of the Diavik Diamond Mine to 2021, although in true mining fashion, further discoveries may well push the date beyond this. However, the company has worked hard to ensure it leaves a positive legacy for the area by building and supporting sustainable local businesses and leaving behind an environment that allows for continued use of traditional lands.